Customer Quality Engineer Job Description
Customer Quality Engineers, Manufacturing Quality Engineers, Customer Support Engineering: How Do You Want to Help Your Company?, Quality Engineers: A Professional Team and more about customer quality engineer job. Get more data about customer quality engineer job for your career planning.
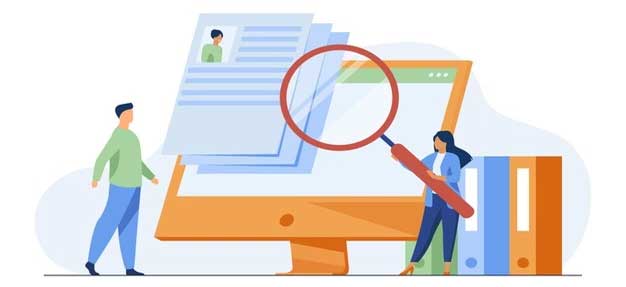
- Customer Quality Engineers
- Manufacturing Quality Engineers
- Customer Support Engineering: How Do You Want to Help Your Company?
- Quality Engineers: A Professional Team
- A Survey of Quality Engineers
- How to write a resume for quality engineer roles in medical device manufacturing
- Customer Quality Engineers: What'll They Do?
- Communication Skills for Quality Engineers
- Customer Service Engineers
- Time Management for Software Quality
- A Certification Exam for Quality Engineers
- The Role of Humans in Quality Assurance
- What is a Quality Engineer?
Customer Quality Engineers
Customer quality engineers need a combination of skills including a background in engineering or materials science, quick problem solving skills and people management skills to be able to address their concerns. Customer quality engineers must have the technical background to analyze problems in the field and help to expedite resolving quality issues for the customer while still being personable and easy to work with when a customer has a problem that has shut down their production line. It is understandable that the customer would be upset at the lost production time when a production line is shut down due to a quality issue.
Shutting down an OEMs is a lot more expensive than dealing with other companies. The customer quality engineer needs to have the technical background to fix the issue while still providing a helpful interface to correct the problem and get their line back up and running. Launching a new product, managing any product changes and final monitoring ongoing quality are the first three phases of the customer quality engineer job.
The customer quality engineer will work with the other engineering groups to make the change to the product design. They will make sure that the change can be produced to the new specification. Testing and inspection will be added to the production process if necessary.
The customer quality engineer will update the documentation to certify the requirements are met. Customer quality engineers help to address quality issues after a product has been shipped by providing direct contact with the customer. They will be able to help resolve any issues the customer has with the company from the location of the label to the non-formance complaint.
They will keep a record of the quality performance at the customer site and watch for deviations from the norm that will be an indicator of a potential problem. It is their responsibility to address issues before they become a serious problem. The customer quality engineer will make sure that the customer is happy with the quality performance that is being provided and that they would be a supplier of choice for future parts.
A nice post on Heating Engineer career planning.
Manufacturing Quality Engineers
Manufacturing quality engineers work industries such as automobile, transportation, textile and industrial equipment and their role is to monitor, test and report on the quality of products. They might inspect raw materials, components, mechanical systems or final products. Quality Engineer responsibilities vary across industries and companies, but the main tasks include testing systems and procedures to ensure they meet technical standards and creating quality and safety documentation.
Customer Support Engineering: How Do You Want to Help Your Company?
Support engineers want to make sure every customer understands the basics of their new product or software service. A customer should feel confident leaving a technical support session because they have the tools to succeed. Customers may have a range of problems.
Customer support engineers need to be calm and patient and recognize that everyone has a different technical background. Carefully talking customers through their problems will help them find a solution as quickly as possible. Sometimes a customer is not alone in their problems.
If a customer support engineer is getting a lot of inquiries about the same problem, it's probably an internal issue. When an issue is internal, it is a good idea to let customers know about it, apologize, and offer an updated version. Everyone makes mistakes.
Keeping customers in the loop shows how honest your company is. Customer support engineers are going to get complaints from angry customers. When a customer issue is beyond the control of the frontline worker, it is time to call a manager.
Customer support engineers should continue to do whatever they can to solve the customer's problem. Their primary goal is still to provide a satisfactory experience for customers. If a customer complaint gets out of hand, it's acceptable to turn it over to a manager.
A nice report on Technical Engineer career description.
Quality Engineers: A Professional Team
A Quality Engineer is responsible for determining production standards for a company's products by establishing quality control systems and setting product requirement rules. Their duties include identifying the specifications for an ideal product, determining an appropriate level of variation and monitoring quality assurance rates. Quality Engineers are employed at companies and organizations that develop physical or digital products.
They are involved in the process of product design and development, creating protocols for production teams to follow that result in high-quality products. Quality engineers are responsible for implementing effective quality controls, teaching production staff how to use them and supervising outcomes. Quality Engineers design automated testing systems and quality control systems to improve the quality assurance process.
They collect data about product errors and investigate possible solutions. Quality Engineers need at least 8 years of experience before they can be considered for senior-level roles. A bachelor's degree can be used as a substitute for 4 years of experience, and a master's degree can be used for 5 years of experience.
Product Engineers and Quality Engineers work together to make new products. Product Engineers are in charge of the general design of the product. They create theoretical specifications of an ideal product, then communicate with Quality Engineers about how to make sure every single product leaves a manufacturing plant is similar to that prototype.
Product Engineers determine the resources needed to turn a product idea into a reality. The Quality Engineer applies the work of the Product Engineer to mass production. They manage the variables that could impact the final product, such as manufacturing conditions, machine behaviors and human error, as well as the flow of products that the Product Engineer designed.
A Survey of Quality Engineers
An associate degree in quality engineering is required for entry-level quality engineers. Some employers prefer candidates with a four-year degree in quality, industrial or mechanical engineering. A master's degree in quality assurance is needed for advancement to management positions.
Career prospects can be helped by certifications. The American Society for Quality has a gold-standard Certified Quality Engineer certification that is one of nine industry certifications that deal with various aspects of quality control practices. Quality engineers work in manufacturing environments and laboratories to test processes and monitor quality standards for all types of manufactured products.
Work environments can be different by industry and establishment. Some of the QEs work from home while others work from a desk and spend their day reading data. Quality engineers are part of a larger team that is tasked with making quality improvements.
Senior engineers may have responsibility across multiple stages of a process. Quality engineers make more money if they have experience in their industry. A quality engineer with five to 10 years of experience can expect to make $70,000 per year, which is a big jump from the starting salary of $63,000.
The industry you work in has an impact on pay. The median salary for a qas in the computer and electronic product manufacturing sector was $94,120 in 2017). Half of the people in the group earn more and half earn less.
Detailed report on Electrical Engineers career guide.
How to write a resume for quality engineer roles in medical device manufacturing
Quality Engineers work within a wider team of professionals to make sure that the final products are safe, reliable and meet customer expectations while keeping the manufacturing process as effective and cost-efficient as possible. Quality engineers can have a specific focus or area of expertise in larger manufacturing operations such as Quality Assurance, Quality Control, Six sigma, Quality By Design, The Taguchi Method, Quality Risk Management or even Reliability Engineering. ISO 9001:2015 is the most widely implemented quality management system.
Quality Assurance uses a number of techniques and methodologies. Quality Engineers can work in an office, on the manufacturing floor, or in a lab, depending on the tasks they are carrying out at the time. Tailoring your Quality Engineer resume to reflect the language used in the job advert is very important.
If you have relevant experience or skills, use the words and phrases that the employer has used to describe them. Do not assume that someone will read the same words. I am not sure if you would best served with it if you are targeting a quality role in medical device manufacturing.
Just apply for roles that are listed and speculatively and see how you fare. Get feedback from people in the industry by networking with them. You should be able to get quality assurance roles without any additional training, but you should know what areas you covered in your undergrad program.
Customer Quality Engineers: What'll They Do?
A customer quality engineer is responsible for all in-process batches. You will be responsible for ensuring that the quality processes are consistent and that the customer root cause audits are done correctly. Other duties include assisting in new product launches, and participating in the control process.
You are expected to relay feedback from customers to the quality management team. You are expected to train the team in identifying and creating methodologies to solve quality issues. The customer quality engineers who went onto college to get a more in-depth education studied electrical engineering and business, while a small group of them studied mechanical engineering and industrial engineering.
Customer quality engineers and process engineer interns have a lot of differences in their careers, but there are some skills that are the same. Both careers require corrective actions, product quality, and continuous improvement. Customer quality engineers reach higher levels of education than process engineer interns.
The process engineer interns are less likely to get a Master's Degree than the PhD interns. A manufacturing engineering intern is responsible for assisting the manufacturing engineers on the plant's daily operations, analyzing the manufacturing process and procedures, and recommending strategic solutions to maximize productivity and minimize costs. Manufacturing engineering interns shadow the production staff, inspect the tools and equipment of the manufacturing, analyze the quality control documentation, and perform related administrative tasks to get a feel for the plant structure.
A manufacturing engineering intern needs to have good communication and organization skills, as well as the ability to adapt quickly to a fast-paced environment. Manufacturing engineering interns earn less education than customer quality engineers. They are less likely to earn a PhD and graduate with a Master's Degree.
Read our report on Firefighter Engineer career description.
Communication Skills for Quality Engineers
80% of the job of Engineer is interacting and communicating with other people if you have good English communication skills. They are communicating with staff, consultants, and Subcontractors. Either way, it is in either email or verbal. The above has helped the beginners on what skills a quality engineer needs to possess and should help them in their quest to become a successful quality engineer.
Customer Service Engineers
Customer service engineers respond to issues in person when they can't be solved over the phone. They discuss problems with clients, perform diagnostic tests on equipment, and work to resolve problems. It is up to customer service engineers to visit client sites and perform tests to prevent downtime from product issues.
They log preventative maintenance visits, run reports detailing what processes were completed, and make notes about what might need to be done in the future to prevent problems. Customer service engineers are often the ones to discuss service contracts with clients. They show the benefits of such contracts, negotiate renewal terms, and outline what services are attached to specific types of contracts.
Detailed post on Structural Engineer job guide.
Time Management for Software Quality
Managing your time well will ensure you have enough time to complete your tasks and confirm they comply with specifications. It reduces stress and makes it easier to complete your duties. When you meet your deadlines, you also make sure others who rely on you have enough time to meet their own deadlines without affecting their work quality.
Problem-solving skills can help you find solutions if you are struggling to meet quality standards. When challenges arise in your duties, a combination of creativity, logic and critical thinking can serve you. Communication skills that are strong can help you explain how to improve processes to other people.
Your listening skills are important for understanding what your colleagues need from you. Strong written communication is a must for software testing and other quality assurance roles. Quality assurance requires understanding quality standards.
Employees are expected to work within the company's standards. Understanding the guidelines set by the Food and Drug Administration can help you meet quality expectations. Supplemental training can teach you new practices and remind you of some techniques you may have overlooked.
A Certification Exam for Quality Engineers
Quality engineers are often working in a manufacturing or laboratory environment with the quality control team to maintain high standards. The engineer is in charge of manufacturing and engineering processes to prevent issues from occurring. You have an associate's degree and work experience to get you certified by the American Society for Quality.
The topics covered in the certification exam are management and leadership, the quality system, product and process design, product and process control, continuous improvement, quantitative methods and tools, and risk management. You must have your knowledge up to date by renewing your certification every three years. Quality engineers play a vital role in the food and beverage industry as they are responsible for the health and safety of consumers and destroy public trust.
Quality engineer jobs are in food and beverage. Quality engineers in the automotive industry work to make sure the vehicles that get us from point A to B are safe and manufactured to specification. There are jobs for a quality engineer in automotive.
Quality engineers in the aviation, space, and defense industry are responsible for maintaining quality standards and compliance with legislation that is detrimental to public safety. Quality engineer jobs are in aviation, space, and defense. Quality engineers in the energy industry work with manufacturers to develop processes, test procedures, implement systems, and analyze efficiency among various types of renewable energy.
Detailed paper on Chief Maintenance Engineer job description.
The Role of Humans in Quality Assurance
If you work in quality assurance, you know how quickly emerging technologies are changing the nature of your work. The internet of things, machine learning, andRFID tracking are just a few of the new disruptive technologies that are almost certainly going to impact your career in one form or another in a few years. Quality assurance is about preventing a bad product from being produced and keeping it from reaching the consumer so that it can do harm.
Quality assurance workers who demonstrate an ability to understand interpret data have an advantage over those who don't. Those who can take the data, boil it down, and use it to communicate with other people have the greatest advantage. Quality assurance processes and protocols can be implemented with project management skills.
When a company makes significant changes to their processes, project management can affect the quality of the process. Implementing any of the technologies poised to impact the work done by quality assurance teams will be no easy feat. Incorporating them in the supply chain will require a solid foundation in project management and a good understanding of both the QA process and the supply chain.
Quality assurance workers should develop specific industry expertise to increase their job security as more of the job is automated through the use of technology. Being effective in quality assurance requires an understanding of how the product affects humans. It requires a sense of what is at stake if bad product leaves a facility.
It requires a level of compassion for the end users. Big Data, machines, and robots are tools. Quality assurance processes will be helped by them.
What is a Quality Engineer?
The process of development, production, and deployment of a good or service is a process that starts with an ideand ends with a product for the customer. The goods or service will function as expected if all goes according to plan. Along the way to correct mistakes, adjustments are needed.
Many businesses have an architecture of plans and processes that oversee the product's life cycle and maintain its quality to mitigate the potential for faulty products. What are the responsibilities of a quality engineer? The job description will tell you what the responsibilities are of the position.
If time allows, you can expand your answer to cover the role that the company plays. You should explain how you understand the issues of the program. How would you argue for a change?
Other stakeholders in the production process may disagree on what is required, even though a QE is expected to provide solutions that improve quality. You have to convince people. You must be tactful yet firm on quality issues as a QE.
What is the importance of a project plan? The quality management plan details the processes and standards that will define a quality product. Without the guidelines there would be no rationale for the actions of a QE.
See also our study on Lead Software Engineer career guide.









X Cancel