Foam Manufacturer Job Description
Syntactic Foams, Polyurethane Foams, High Density Foam Sheet, Why did the USCG not allow a ship to dock?, Good Manufacturing Practices and more about foam manufacturer job. Get more data about foam manufacturer job for your career planning.
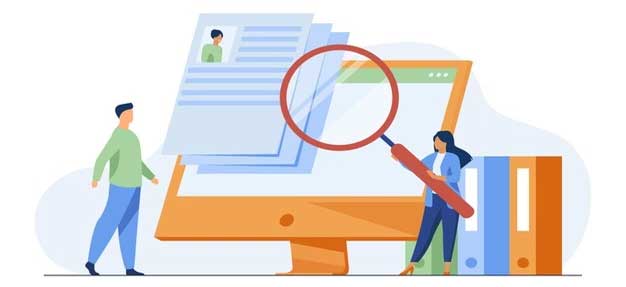
- Syntactic Foams
- Polyurethane Foams
- High Density Foam Sheet
- Why did the USCG not allow a ship to dock?
- Good Manufacturing Practices
- The Rise and Fall of Manufacturing
- NomaGreen Natural: A Bio-Based, Closed Cell Polyethylene Foam
- Detection of the Violations in High-Energy Nuclear Collisions
- Ear Muff vs Foam Emulsion for Manufacturing Facilities
- The Effects of Environment on the Installation and Performance Of Foam
Syntactic Foams
A bath sponge and a beer head are examples of foams. The foams have thin films of liquid or solid that separate the regions of gas. suds are also known as soap foams.
Solid foams can be closed or open. The gas forms pockets in closed-cell foam that are completely surrounded by the solid material. Gas pockets connect to each other in open-cell foam.
An open-cell foam is an example of a bath sponge that can be easily washed. A closed-cell foam camping mat has gas pockets that are sealed so the mat cannot absorb water. The thickness of the film for metastable foams is lower than the bubble and can be considered a network of films.
The lamellae should connect in the middle of the three main areas of the body and then go outward from the connection points. Van der causes the stabilization of a foam. The Marangoni effect, which acts as a restoring force to the lamellae, is caused by the waals forces between the foam and the double layers of dipolar surfactants.
The Marangoni effect depends on the liquid being foamy. The surface tension is usually decreased by the use of surfactants. The surface of the surfactants is covered with a layer.
See our article on Light Manufacturer career planning.
Polyurethane Foams
The reaction of polyols and diisocyanates makes up the synthetic material of Polyurethane foam. Its structure is made up of two phases. The solid phase is made from a material called polyurethane elastomer.
The gas phase of foams has many desirable properties such as good thermal and acoustic insulation, high force absorption, and flexibility. foam rubber is a term used for the foams. Flexible and rigid foams are the main types of foam.
Flexible foams can be made from either polyether or polyols. They have lower bulk densities. Flexible foams are used in furniture, seat cushions, mattresses, and acoustic dampers.
High Density Foam Sheet
The high density foam sheet has unique design capabilities. The design engineer can use high-density EVA foam as stiff as a pretzel or as flexible as macaroni. Product performance can be explored with the treasure trove of possibilities. There are sheets, rolls, foam tape and buns.
See our paper about Rubber Manufacturer career guide.
Why did the USCG not allow a ship to dock?
A ship was to arrive in the US after a long voyage. A foam sample was sent for testing. The foam sample analysis results were received three days before the arrival.
Why did the USCG not allow the ship to dock? They must have felt that it was dangerous to allow the tanker to come with an ineffective foam system. The foam is created by mixing foam concentrate with water.
A correct amount of water and foam concentrate is needed for the effective generation of foam that can be used in firefighting. In 2009, the foam testing requirements were revised because it was found that foam concentrate with alcohol may not extinguish the fire as desired. The foam is injected into the fire water to form a solution.
The proportioner will either inject more foam or less foam if it is not set correctly. The system will be less effective in both cases. The foam will not run for the time it is supposed to run if it is injected more.
The foam generated may not be effective in extinguishing the fire if it is injected less. The article is very good and covers foam concentrates. It is important to test at least yearly because of the degradation of the concentrate overtime.
Good Manufacturing Practices
Candidates with the ability to write and understand code are sought by many manufacturers. Companies that have experience with coding and software development may be able to transition into more digital methods. Manufacturing companies often seek candidates with experience with manufacturing specific devices and machines.
Good manufacturing practices are those that have a technical ability to supervise quality. Ensuring that a manufacturer creates products with consistency is helped by the standards of the Good Manufacturing Practices. They make sure each product is of the highest quality.
See our post on Candy Manufacturer career guide.
The Rise and Fall of Manufacturing
Manufacturing has made a comeback since the recession ended. Since 2010, there have been nearly one million new production jobs. There are more job openings, but not many young people are prepared to take them. With half of the current manufacturing workforce age 45 or older and nearing retirement, manufacturers need younger employees more than ever.
NomaGreen Natural: A Bio-Based, Closed Cell Polyethylene Foam
NomaGreen Natural is a bio-based, closed-cell polyethylene foam made from sugar cane, a renewable resource, yet retains the performance characteristics of standard polyethylene foam. NomaGreen Natural can be recycled in the standard LDPE recycling stream, as it has an indefinite shelf-life.
Detailed post about Plastic Manufacturer career description.
Detection of the Violations in High-Energy Nuclear Collisions
The technical information provided by the manufacturer will allow us to develop suitable controls and wear protective equipment to protect us against the dangers associated with machines and equipment.
Ear Muff vs Foam Emulsion for Manufacturing Facilities
Most manufacturing facilities have their own issues that they need to address. Ear Muff style hearing protection can cause headaches and foam ear plugs aren't always adequate in preventing all frequencies in getting through. The ability to communicate effectively with either style of hearing protection requires removal and short time exposure to sound and shouting in a loud environment, which is one of the issues.
Hearing loss can be caused by short bursts of loud sound. The foam earplugs are inexpensive, light to carry around and great in all weather. They aren't particularly effective with loud equipment found industrial environments and manufacturing equipment.
See also our paper on Medical Manufacturer career planning.
The Effects of Environment on the Installation and Performance Of Foam
There has been a dramatic increase in the use of foam and a disproportionate increase in the number of foam installation problems, but not all of them are related to the foam material itself. Assembly and performance problems can be caused by design errors, material choice errors, or changes in environment. Chemicals leave the factory and can cause chemical problems.
The chemicals must be kept in good condition during shipping and storage. Chemicals that are past their shelf life can be a cause of foam problems. Some products need to be mixed to avoid separation of the chemicals, and some chemicals can lose their add-ons over time.
If the equipment is partially restricted or not maintained, the foam can be hard and brittle, or sticky and soft, depending on the chemical component balance. Chemicals that are too cold or hot can cause off-ratio processing. Success still isn't guaranteed even if foam is mixed with good quality chemicals
There are a variety of defects that can be caused by improper application or failure to allow for changes in environmental conditions. When foam can be installed and how it is cured can be limited by cold weather. It is not recommended to install foam in ambient or cold conditions.
The cure period may need to be controlled to avoid thermal shock and delamination. The installation season can be extended with temporary heat and insulation. The foam that is sprayed onto the cool substrates may not bond correctly, and it will have a high density.









X Cancel