Inventory Auditor Job Description
The Inventory Auditing Position at a Large Retail Company, Verification of Stock Records by Auditor, Inventory Auditors, Inventory Auditors, Inventory Auditing and more about inventory auditor job. Get more data about inventory auditor job for your career planning.
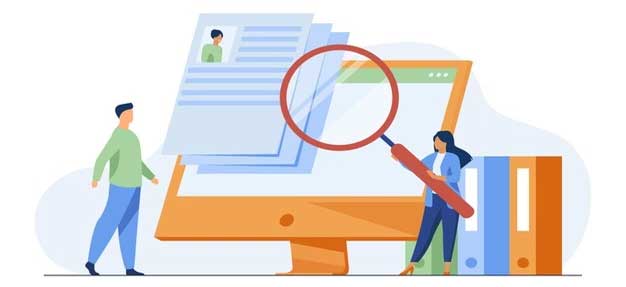
- The Inventory Auditing Position at a Large Retail Company
- Verification of Stock Records by Auditor
- Inventory Auditors
- Inventory Auditing
- Inventory Audit Job Description
- Physical Inventory Counting
- An Inventory Auditor
- Warehouse Inventory Specialist Job Description
- ShipBob: Inventory Auditing Software for E-Retail Stores
- Counting Inventory in Retail Stores
- An Inventory Clerk Position in a Heavy Machinery Environment
- Inventory Count Reconciling to the General Ledger
- Managing Inventory in Business
- Auditing Inventory
The Inventory Auditing Position at a Large Retail Company
Independent inventory audit firms work for large retail companies. Their duties include matching the physical count to the computer inventory. The computer data for the planning and forecasting groups is maintained by auditors.
The auditor reports to the supervisor. The inventory auditors are not surveyed separately by the Bureau of Labor Statistics. The auditor position is responsible for counting all physical inventory, generating audit reports, reconciling computer data with physical counts taken, and reporting on errors found.
The position works with each department to suggest ways to reduce errors. The inventory auditor performs audits of paperwork at the receiving dock, each department transfer area, and any outbound areas, such as shipping or layaway. Excellent communication skills, both oral and written, and experience inventory counting are required for the position.
See also our post about Inventory Management career planning.
Verification of Stock Records by Auditor
3. The stock records may be checked by the auditor and the management may use a system of physical verification to verify inventories. The entries such as receipts, and issues in the stock records can be verified with the Goods received notes, inspection reports, material issued notes etc. The amount of examination depends on the reliability of the internal control procedure and the results of the auditor's examination of stock records.
Inventory Auditors
Inventory auditors travel frequently to different stores to record accurate counts of various products and materials. Delivery companies, suppliers, inventory management companies, and retail businesses all hire inventory auditors to work full-time shifts that may include nights and weekends, along with some potential overtime. Inventory auditors work in warehouses and retail stores.
They work independently most of the time and report to their supervisors. Inventory auditors check for expired merchandise and other issues that may affect quality. They report issues with inventory such as shortages, overages, and damaged items.
A nice paper on Retail Inventory Specialist career guide.
The requirements to get a job as an inventory auditor are similar to other entry level positions. You only need a high school degree to get a formal education. Inventory auditors deal with correspondence, be it with managers or suppliers.
Knowing how to use email and word processing is required. Knowing how to use a database program is an essential skill for an inventory auditor. Good physical condition is a must for inventory auditors, who work in retail and warehouses.
They lift items and packages as much as 50 pounds. They may have to climb ladders to get to the top shelf and also lift and return things from there. An inventory auditor's primary concern is to make sure that entries in the database match the actual count.
It is a daily task to make sure that everything is counted right and it requires a level of concentration. Getting things right during inventory is important for other departments. The purchasing, planning and forecasting team needs data gathered by an inventory auditor in order to proceed with a plan of action.
Inventory Auditing
Inventory auditors compare inventory records to physical inventory to make sure the numbers match. As an inventory auditor, you have to count stock quantities, review records and document any discrepancies. You may be required to determine why there may be missing products or why figures were miscounted, and advise your employer on ways to limit future inconsistencies.
Don't miss our column about Staff Auditor career description.
Inventory Audit Job Description
Every time they go to work, the inventory audit job description makes a difference. We can help you find more than 205 inventory audit job description so you can choose a career path that will give you a sense of personal fulfillment.
Physical Inventory Counting
Responsible for counting all physical inventories, generating audit reports, reconciling computer data with physical counts and reporting on errors. Also performs inventory audits.
Read also our column on Inventory Analyst career planning.
An Inventory Auditor
An experienced Inventory Auditor with a keen eye. Accurate inventory reports are helpful in the budgeting process and in reducing loss due to theft. Specializes in technology and home appliances.
Warehouse Inventory Specialist Job Description
Are you analytical person who wants to figure out the root cause of the problem? A warehouse inventory specialist job is a good one. A warehouse inventory specialist wants to ensure accuracy of inventory within the warehouse and within its software systems.
They are the main points of contact when there is an inventory problem. Warehouse inventory specialists are responsible for maintaining inventory control, resolving inventory issues, and ensuring accurate inventory counts. They identify and coordinate with inventory control managers to make process improvements.
A warehouse inventory specialist can be involved in purchasing and delivery schedules. They will perform any other warehouse duties as needed. The hiring manager will want to observe the warehouse operations and inventory control processes of the candidate.
Read also our post about Materials Sourcing And Purchasing Agent And Inventory Control Assistant job guide.
ShipBob: Inventory Auditing Software for E-Retail Stores
An inventory audit is a process of checking a company's actual inventory levels against their financial records to ensure accurate inventory accounting. An inventory audit can be performed by the company or an outside auditor to find out if there are any problems with the accounting methods. They can be as simple as counting physical stock levels and cross checking against records, or as complex as hiring a third party auditor to assess all of your inventory procedures.
If there are discrepancies in your inventory audit, you may want to reconcile items to find the root cause. You should keep an eye on the error-prone SKUs in the future. An efficient inventory management process can help reduce the number of audits.
Physical retail stores are different from e-retail stores as sales can take place anywhere across the globe and are more unpredictable. If you don't have an accurate method for keeping track of your inventory's value, you can't budget for the next batches of inventory Inventory audits can help you budget better and more accurately when you know the exact inventory count you have and how much safety stock you should keep.
It is very difficult to audit physical inventory. If you sell 500 SKUs and you check actual inventory levels against the amount of inventory you have listed on hand electronically or in an inventory sheet, that can take days to complete. If you have one or more units, you will spend a while on a manual task.
It is important to go electronic with inventory reports to save time. 3PLs like ShipBob help with this. When the system marks the product stock as zero, it can prompt a spot check to make sure there are no more units in hand.
Counting Inventory in Retail Stores
It can be hard to get training to become an inventory auditor. The techniques and procedures used to count inventory are specific to the business. If you have a familiarity with retail business, computers, and hand held calculators, you will be able to become proficient as an inventory auditor for RGIS.
Inventory work is not hard physical labor but it is a taxing mental process. You should have a good knowledge of the counting process in the section of the store that you are assigned to. tags that indicate an area has already been counted
A white tag is placed in the section showing the total count and initials of the person who did the counting. After all information has been downloaded into the man computer system, you should be involved in retrieving the tally sheets and removing the inventory tags. When you are told to do so, begin pulling tags.
A nice post on Inventory Specialist career guide.
An Inventory Clerk Position in a Heavy Machinery Environment
An inventory clerk is a person who monitors product levels and ensures there are enough supplies to meet the company's needs. Their primary duties include accurately tracking inventory data, solving discrepancy problems and analyzing previous data to help a company make informed decisions. An inventory clerk is responsible for ensuring the stock in the company is always available.
They must anticipate future stock needs. The inventory clerk should always be looking for ways to make the stock count more accurate. The person applying should have experience working with large amounts of inventory in a shop, parts department or distribution facility.
If you haven't dealt with stock rooms, look for a candidate who has worked in retail such as a Retail Buyer or Shop Assistant. An application that has experience observing consumer trends and seeing how certain products are sold within an industry will have a good understanding of the supply and demand necessary within the industry. The average salary of an Inventory Clerk in the UK is over twenty grand per year.
Experience, location and company are the main factors that affect salary. An inventory clerk needs to be prepared for fast paced and chaotic environments. They will most likely be assigned to work in a warehouse or stock room and have access to an office for administrative purposes.
They must be prepared to work with heavy machinery, such as a forklift, pallet jacks, jib cranes, conveyor, vertical carousels and more. The Inventory Clerk is reporting to the Inventory Manager. The inventory clerk may have to report to their manager on a daily basis or only when there are discrepancies in the inventory.
Inventory Count Reconciling to the General Ledger
The inventory count should be Reconcile to the general ledger. They will trace the valuation from the physical inventory count to the general ledger to make sure the balance was carried forward into the company's accounting records. Test high-value items.
If there are items in the inventory that are of high value, the auditors will spend more time counting them inventory and making sure they are valued correctly, and then tracing them into the valuation report that carries forward into the general ledger. The test item costs are not known. The auditors need to know where the costs come from so they can compare them to the costs listed in the inventory valuation.
Review freight costs. You can either include freight costs inventory or charge it to expense, but you need to be consistent in your treatment so the auditors can see how you handle freight invoices. Test for a lower cost market.
The auditors must follow the lower of cost rule and compare a selection of market prices to their recorded costs. The finished goods cost analysis done. If a significant proportion of the inventory valuation is comprised of finished goods, the auditors will want to review the bill of materials for a selection of finished goods items to see if they show an accurate compilation of the components in the finished goods items, as well as correct costs.
Direct labor analysis. If direct labor is included in the cost of inventory, the auditors will want to trace the labor charged during production time cards or labor routes to the cost of inventory. They will look into whether the labor costs listed in the valuation are supported by payroll records.
A good study about Inventory Control career description.
Managing Inventory in Business
Most business owners are scared to death when they read the wordaudit. Understanding the nuances of an inventory audit ahead of time will prepare you for what will come and set you up for success. An inventory audit is when either you or an auditor uses analytical procedure to check a company's inventory methods and confirm that the financial records and actual count of goods match.
It is important to conduct inventory audits to ensure that you have the right amount of stock at the right time. You will know what products you have on hand if you understand stock flow. An internal employee or external auditor will conduct a series of procedures to verify your records if your inventory undergoes an audit.
Any stage of operations can include procedures for inspection, observation, confirmation, recalculation, performance, or analytical analysis of inventory. An efficient inventory management process can help reduce the length of audits. If you have a system that tracks items when they come in and out of your store, there will be time stamps associated with each action that can be tracked easily.
Auditing Inventory
Auditors need evidence to verify the validity of financial records. It can either verify or provide support for the financial information presented. The evidence can show that the financial information is incorrect.
Auditing inventory must verify the amount of inventory, its quality and condition, and whether the value is represented in financial records and statements. An ABC analysis includes grouping inventory. High-value inventory, mid-value, and low-value products can be grouped together.
The items can be tracked and stored in different groups. The freight cost analysis used to determine the shipping or freight costs for transporting inventory. It is important to track the freight costs because they are included in the value of inventory.
Matching involves matching the number of items and the cost of inventory shipped. Auditors can conduct matching to verify that the right amount was charged. Overhead analysis includes analyzing the costs of business overhead that may be included in the costs of inventory.









X Cancel