Materials Manager Job Description
The Materials Manager in a Large Chemical Company, Materials Managers: A Career Path in Business, Managers of Materials, Purchasing Managers, Materials Managers: A Career Path in Supply Management and more about materials manager job. Get more data about materials manager job for your career planning.
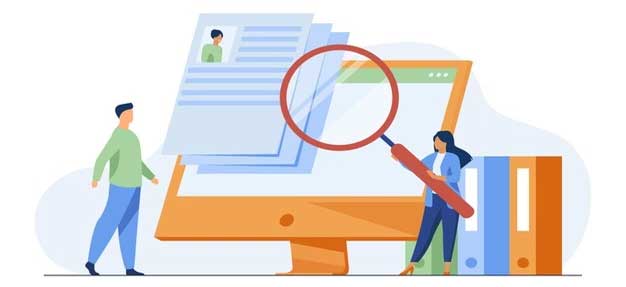
- The Materials Manager in a Large Chemical Company
- Materials Managers: A Career Path in Business
- Managers of Materials
- Purchasing Managers
- Materials Managers: A Career Path in Supply Management
- The Materials Manager of the SU(2) PLC
- The Material Manager for a Chemical Company
- How to Be Successful in Leadership Training
- The Materials Manager in a Central Store
- The Material Manager
The Materials Manager in a Large Chemical Company
The materials manager helps the company in attaining both their long and short term general goals and also in making sure that the company's supply chain is functional at every given point in time. The manager works with the human resource unit to interview and train qualified staff for the materials management unit.
Read also our report on Production Manager career planning.
Materials Managers: A Career Path in Business
The materials managers are tasked with managing the inventory of supplies. They work with other managers to determine what the business needs and then use complex budgets to decide what should be ordered. They ensure that new supplies are allocated correctly and that the receiving process is smooth.
A materials manager may be asked to maintainventory so that customer orders can be fulfilled in a timely fashion. They are tasked with maintaining relationships with suppliers and looking for new and better ways to get raw materials at a lower price. Materials managers will need to purchase supplies.
A master's degree in a business-related field is a good way to further your career path. The on-the-job experience is more beneficial to furthering a materials manager's career than education beyond a bachelor's degree, but check specific materials manager position descriptions for more details. Most materials managers will use the internet for ordering, but they are also likely to have deep personal connections with suppliers and might rely on traditional sales techniques.
They should be proficient in Microsoft Office and internet use. Materials managers typically require the use of spreadsheets and in-house database programs. Better Team explains that materials managers are often referred to as purchasing managers due to their role as a buyer.
Managers of Materials
Managers of materials have experience inventory control. They have excellent organizational and record-keeping skills. The ideal candidate should have attention to detail and problem-solving skills.
See also our report about Home Manager career guide.
Purchasing Managers
A materials manager is supposed to coordinate the planning and coordination of the company's inventory and purchasing departments. They are tasked with researching the best prices, monitoring inventory levels, and negotiating contracts. Purchasing managers are also known as purchasing managers.
Materials Managers: A Career Path in Supply Management
A materials manager is a person who oversees a company's needs for inventory and supplies. Their duties include training operations staff, signing purchase orders and tracking inventory through the supply chain. Materials Managers are usually in warehouses so they can have a hands-on approach to maintaining inventory levels.
They are the main point of contact for vendors and they are responsible for negotiating the terms of supply contracts. Managers explain the distribution process to their team to improve reliability and quality. The price of a product is set by the materials managers, who make adjustments to account for changes in the cost of attaining, storing and transporting materials.
Depending on the size of the organization, the educational requirements for a Materials Manager position can vary. A high school degree is not enough for most businesses, they need a bachelor's degree. Material Managers can get certifications from organizations such as The American Purchasing Society, The American Production and Inventory Control Society, The Next Level Purchasing Association, The Universal Public Procurement Certification Council, and The National Institute of Government Purchasing.
Materials Managers coordinate high-level logistics while Inventory Clerks handle the small details and day-to-day upkeep of inventory organization. Inventory clerks can work with a specific type of material, like only working with finished products, while materials managers can purchase all the raw goods, packaging and equipment needed for production. Materials Managers assign tasks to Inventory Clerks.
Material Managers travel to make deals and inspect materials while inventory clerks work on the floor. Successful materials managers are organized and practical people who understand how scheduling and logistics can impact a business. They are passionate about finding better ways to achieve a result.
Read also our study on Hospitality Manager job description.
The Materials Manager of the SU(2) PLC
The Material Manager is responsible for the supervision and facilitation of all the actions related to the acquisition of materials, supplies, equipment, and services required for the company departments to perform their contractual base life support. Oversees the proper packaging, approvals, and routing of all purchase requisitions for purchase, as well as, post-entry supply chain tracking and maintaining comprehensive files documenting all purchase requests. The Materials Manager is expected to perform with minimal supervision and take ownership of the warehouse operations, even though he reports to the Supply Chain Director.
The Materials Manager is responsible for monitoring production in accordance to guidelines set by operations management of the plant to work to get the most efficient output of production in the most convenient manner. They have to monitor and manage all inventories to make sure they have accurate information. Responsible to submit reports to the company.
The Material Manager for a Chemical Company
They are most likely to oversee procurement, storage, planning, control, and distribution of various materials and products for the company. The experts need to have some experience inventory control. You need to help companies find the supplies they need.
You have to work with the production and purchase departments. The manager helps the company achieve its goals. They need to make sure the supply chain is running.
They are responsible for coordinating and planning the process of buying materials. The manager is mainly involved in development requests and the supply acquisition process. They need to keep a record of the purchases that the company makes.
The manager can't meet all the supply's needs so they need a team to help them with regular duties You need to have some skills to be a materials manager. You must have leadership skills as well as great communication and Interpersonal skills.
Read also our paper about Government Affairs Manager job planning.
How to Be Successful in Leadership Training
The pro tip is to always be on the lookout. Do you need help with management skills? Leadership training programs can help you get your talents noticed. They are not a substitute for achievement, but they will help an entry-level manager stand out.
The Materials Manager in a Central Store
The materials managers are responsible for buying products. Ensuring material flow in a manufacturing unit, developing requests for proposals, acquiring supplies, and implementing purchasing policies are some of the duties mentioned in typical resume samples. They keep documentation and create a budget for the department.
Material managers look for the best deals for a company, and look for the best quality material at the lowest possible cost. The main duty of a material manager is to plan, control and lead the personnel and activities of a central store operation. They provide a point in lean manufacturing training and perform cycle counts.
The material managers are also in charge of the budget. The material manager will get the goods and place them in the inventory to make sure the proper department gets them on time. A minimum of 2 to 3 years of experience in material management is required for undergrads in the same fields.
Larger companies may require more experience in order to get the position. The core supply chain function is materials management. Firms use materials management to plan their total material requirements.
The material requirements are communicated to the procurement and other functions. The materials management team is responsible for determining the amount of material to be deployed at each stocking location across the supply chain, establishing material replenishment plans, determining inventory levels to hold for each type of inventory raw material, and communicating information regarding material needs throughout the extended supply chain. The primary goal of Materials Management is to assure supply of material, optimum inventory levels and minimum deviation between planned and actual results.
A nice paper on Analytics And Insight Manager career description.
The Material Manager
The Material Manager is responsible for determining the right amount of materials and products to hold in the warehouse and for managing inventory, warehouse storage, distribution and replenishment plans.









X Cancel