Materials Technician Job Description
Materials Managers: A Career Path in Logistics, Testing materials for improved products, Materials Engineers, Laboratory Technicians, Strategic Communication for Job Descriptions and more about materials technician job. Get more data about materials technician job for your career planning.
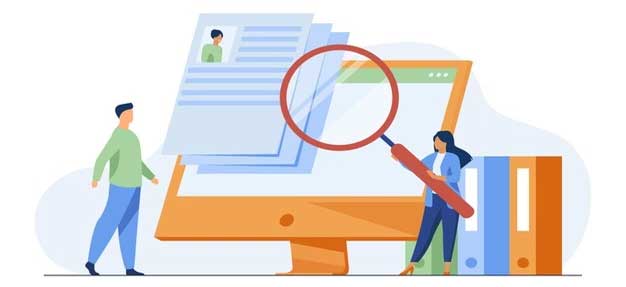
Materials Managers: A Career Path in Logistics
A materials manager is a person who oversees a company's needs for inventory and supplies. Their duties include training operations staff, signing purchase orders and tracking inventory through the supply chain. Materials Managers are usually in warehouses so they can have a hands-on approach to maintaining inventory levels.
They are the main point of contact for vendors and they are responsible for negotiating the terms of supply contracts. Managers explain the distribution process to their team to improve reliability and quality. The price of a product is set by the materials managers, who make adjustments to account for changes in the cost of attaining, storing and transporting materials.
Depending on the size of the organization, the educational requirements for a Materials Manager position can vary. A high school degree is not enough for most businesses, they need a bachelor's degree. Materials Managers coordinate high-level logistics while Inventory Clerks handle the small details and day-to-day upkeep of inventory organization.
Inventory clerks can work with a specific type of material, like only working with finished products, while materials managers can purchase all the raw goods, packaging and equipment needed for production. Materials Managers assign tasks to Inventory Clerks. Material Managers travel to make deals and inspect materials while inventory clerks work on the floor.
Successful materials managers are organized and practical people who understand how scheduling and logistics can impact a business. They are passionate about finding better ways to achieve a result. Good Materials Managers are great teachers and mentors who can delegate tasks to their team and explain clear expectations about the quality and speed of their work.
See our paper about General Maintenance Technician career description.
Testing materials for improved products
You would conduct tests on materials to see how they can be used to improve products. Your work would mean a higher standard of goods would be produced more quickly and people would be able to buy them cheaper.
Materials Engineers
Materials engineers and materials technicians work together to test materials. They look at the performance of materials used in machinery and structures to find flaws and other problems. Materials technicians can test materials to eliminate faults, improve the qualities of existing materials, and assess the safety and environmental impact of materials.
They may work in the construction, transport, metal fabrication and manufacturing industries. Non-destructive testing techniques, such as X-rays, can be used to find internal faults in structures. They can inspect welds with fibre optic cameras.
Don't miss our column on Security Systems Technician career planning.
Laboratory Technicians
Lab technicians have extensive knowledge of the methods, procedures and techniques used to perform laboratory tests and analyses, as well as of all the relevant laboratory equipment and instruments. They are familiar with the methods used to record and present data. The responsibilities of a laboratory technician include maintaining lab instruments, as well as conducting periodic tests to ensure they function efficiently and accurately.
The laboratory has to have everything it needs to operate, so it is important that the technicians check the stock of materials. They can give advice to the laboratory's scientific personnel on the correct use of equipment, and evaluate the introduction of new methods and instruments. Laboratory technicians work in chemical analysis laboratories where they perform quality control tests on raw materials and intermediate products industries such as the manufacturing of pharmaceuticals and cosmetics.
Laboratory technicians work in hospitals, clinics and other healthcare facilities. A technician in a laboratory performs analyses on bodily fluids and blood and performs immunological tests. Depending on the workplace, the working hours of a laboratory technician may be different.
Lab technicians may be required to work shifts, including nights, in some areas, such as the industrial and pharmaceutical sectors, where continuous production may be in place. To become a lab technician, candidates will need a technical diploma from a college or school with an emphasis on sciences. Many companies prefer candidates with a degree in a science subject, such as chemistry, pharmaceutical chemistry, biology, biotechnology, chemical engineering or material sciences.
In addition to scientific knowledge, aspiring laboratory technicians need a knowledge of testing procedures and protocols, the ability to use laboratory instruments and equipment without supervision, and familiarity with software applications used for collecting data, documenting test results and producing reports. A lab technician's career will usually start in a position such as laboratory assistant, where they will gain experience in the role and familiarity with all the relevant testing and analytical procedures and laboratory equipment. It is a good career choice for accurate, precise, highly-organized individuals who feel at home in a lab.
Strategic Communication for Job Descriptions
Your job materials are not forms to fill out, but strategic and persuasive communications that will need to be tailored for each potential employer and at every phase in your career.
See our column on Financial Management Technician career planning.
Job Description for a Quality Technician
Quality technicians look for flaws and deviations from original specifications when examining materials and products. They have many responsibilities, including reading specifications and blueprints, making recommendations for adjustments to assembly and production processes, inspecting and testing materials and products, and reporting on inspection results. The qualities needed to do the job are included in a quality technician job description.
Quality technicians need to have outstanding dexterity so they can sort through items quickly and remove parts they need during the manufacturing process. Jobseekers want to know what a job entails before applying, like you want to know an applicants experience before extending a job offer. The job responsibilities section of your quality technician job description is fundamental.









X Cancel