Mold And Die Engineer Job Description
Apprenticeships in Product Design and Development, Resume Sample for a Tooling Engineer, Injection Molding, Plastic Engineer in the Automotive Industry, Design and fabrication of rubber molded parts and more about mold and die engineer job. Get more data about mold and die engineer job for your career planning.
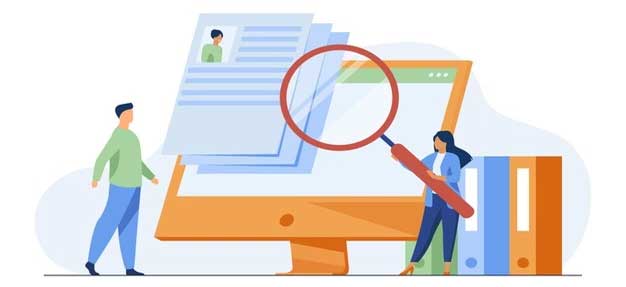
- Apprenticeships in Product Design and Development
- Resume Sample for a Tooling Engineer
- Injection Molding
- Plastic Engineer in the Automotive Industry
- Design and fabrication of rubber molded parts
- Injection Mold Design and Construction
- How to Make a Resume for Manufacturing Engineer Jobs?
- Design and Construction of a Good Core for Injection Mold
- Design and Analysis of Metal Powder Injection Mold
- Die Spotting Press with Rolling Bolster
Apprenticeships in Product Design and Development
A design engineer works to improve performance through research. Their duties include researching new materials and testing prototypes. A design engineer looks for ways to improve a product.
They work with members of the design department to research different product materials, find new approaches to design and try new methods to produce a better product in a more efficient manner. Some companies prefer candidates who have completed an apprenticeship for product design and development. A candidate must have at least four or five grades at grades 9 to 4 to be an apprenticeship candidate.
A design engineer can work in a variety of industries, the type of industry they work in will dictate the products and processes they work on. Construction, renewable energy, electronics and medicine are some of the industries. An application must be able to show much they know about the industry they are applying to.
Both types of engineering want to produce the highest quality product in the most efficient manner. A design engineer is focused on the individual components and materials of a product. A Manufacturing Engineer is focused on mass assembly of the product.
See also our article about Diversity And Inclusion Specialist job guide.
Resume Sample for a Tooling Engineer
The design and development of tooling is managed by tooling engineers. A tooling engineer is responsible for creating drawings, implementing and tracking projects, using dedicated software, overseeing the building of tooling, and launching tooling into production. Skills such as engineering expertise, creativity, drawing skills, time management, decision-making, and computer proficiency are some of the skills that should be mentioned in a resume sample for a tooling engineer. A Master's Degree in engineering is a must have for eligible resumes in the field.
Injection Molding
Injection molded plastic parts are used for mass production. It involves the injection of molten plastic into a mold to make a part. Injection molded objects have been around since the 19th century.
Injection molded parts are everywhere, from the keys on your keyboard to the dashboard of your car. Injection molded plastic parts are often cheaper than other plastic parts at scale, and are often repeatable. It is referred to as volumes ranging from thousands to hundreds of thousands of parts.
It has the highest variety of materials, colors, and cosmetics of any other manufacturing facility. The runner is a channel that connects the plastic material from the screw feed to the part. Plastic will be able to be hardened within the runner channels and the part cavities in a cold runner mold.
Runners are ejected when the parts are thrown. Runners can be sheared off with manual procedures. Some cold runner systems use a three-plate mold to separate the runners and part from one another.
Feed material is kept in a melted state up to the part gate, which makes hot runner molds useless for attaching runners. Sometimes called "hot drops," a hot runner system reduces waste and enhances mold control at an increased tooling expense. The plastic enters the mold through the spouts, which intersect with a runner that leads to the gate.
Read also our article about Kitchen And Bath Designer job description.
Plastic Engineer in the Automotive Industry
A young energetic plastic engineer with over 3 years experience in plastic injection molded is looking for a position to serve for the organisation, learn grow and explore new height with your organisation. 2. The Motherson automotive technology and engineering is a manufacturer of all types of automobile components. Also achieved 5 S and 100 ppm.
Design and fabrication of rubber molded parts
The process of making rubber molded objects is accomplished by either extruding, pressing or pouring a liquid into a mold. Most rubber products are made from rubber with sulfur at high temperature. A block of rubber is used to represent the desired geometry of a molded rubber part.
The rubber material is cured by applying heat energy which causes a chemical reaction. The parts that are manufactured by rubber mold include O-rings, seals, grips, caps, covers, hose adapters, gasket, buttons, handles, knobs, roller, bumpers, and many other. Any 2-D shapes of shallow depth are possible.
When designing your part, you should consider where the die line will be on your part. Define the location and minimum draft angle for your job shop. The more draft the better for some very soft rubber materials.
Attempt to keep your part geometry symmetrical and wall thickness uniform and avoid sharp corners and other geometries that result in an area that will cool slower or faster than adjacent areas. Features that cool slower will have larger dips or craters for selected materials. The post molded part can be molded into inserts or other parts.
A nice column on Telecom Engineer job guide.
Injection Mold Design and Construction
Injection mold is a high-precision manufacturing process that injects molten plastic into a mold, where the plastic cools and becomes a part or product. The piece is ejected from the mold and sent on for secondary finishing. The plastic flows through channels called runners into the mold.
The direction of flow is controlled by a gate at the end of each channel. The runners and gates must be designed to assure the distribution of plastic. The placement of cooling channels in mold walls is important for cooling to create a final product with homogeneity of physical properties.
There areas of weakness that affect repeatability that can be caused by uneven cooling. Construction standards are reviewed and verified after the completion of detailed tool drawings. The tool builder has meetings held on site.
The mold is inspected against a list. A process that is acceptable to the manufacturing department is established. The parameters are established.
Sampling using scientific practices is done, and the filling profile is determined by the pressure transducers in the mold. The parts are qualified. Design engineers must consider steel brittleness.
How to Make a Resume for Manufacturing Engineer Jobs?
Your resume is large and has a big job to do. It is not what you think. Manufacturing engineering jobs are on the rise.
They will grow 8% in the next 10 years. Shrinking pay and tiring work are the problems. You can change the manufacturing engineer resume example to fit any manufacturing engineer position.
You will get 888-353-1299 A manufacturing engineer with over five years of experience designing processes and automation. Seeking to improve product quality and reduce costs.
Savings of 1.5 million dollars were achieved by increased weekly throughput at Logic Brisk. Design is important. We assume the rest is chintzy if the doors rattle and the air flop.
It is the same with a resume. You will look phoned-in if you use the wrong fonts or are too small. You can't look like that and still get interviews.
Read also our story about Structural Project Engineer career guide.
Design and Construction of a Good Core for Injection Mold
The mold base is an important part of injection mold, it can be made by the mold maker or purchased from a standard mold base. When there are undercuts on the design and construction of a good core, it can increase the life of tooling, reduce material consumption, reduce dependence on maintenance inserts, and reduce the cost of making the mold.
Design and Analysis of Metal Powder Injection Mold
Injection speed and product quality are related. A stable melt surface speed can be ensured to produce desired molecule and the smallest internal stress by determining the beginning, middle, and end of the filling speed segment. A metal powder injection mold was designed according to the structural characteristics of parts.
It focused on research and analysis of molded parts, gating system, side core pulling mechanism, fixed distance parting mechanism, demolding system, temperature control system and exhaust system. Problems of heavy blank weight, difficult feeding and difficult demolding are solved by the use of fixed mold inclined top and fixed mold "T"-shaped buckle lateral core pulling structure. The results show that the product's multidimensional accuracy reaches IT5 and the surface value is Ra0.8m.
Warpage deformation is a common defect injection molded thin-shell plastic parts because it involves accurate prediction of amount of warpage, and different warpage laws of injection molded parts of different materials and different shapes are very different. Product assembly is affected when amount of warpage is greater than allowable error. Injection molder barrel needs to be cleaned or disassembled before the machine is used for the first time, or when raw material is changed, color is changed or plastic is found to be decomposing.
A good article about Propulsion Engineer career guide.
Die Spotting Press with Rolling Bolster
The Die Spotting Press with Rolling Bolster has a variety of bed sizes, daylight openings, and down-acting capacities to choose from. The shuttle bolster allows easy crane loading.









X Cancel