Operational Excellence Manager Job Description
Operational Excellence, The Imprints of Operational Excellence on Business Process Improvement, The Operations Excellence Manager at Silica, What Do You Think About Operations Managers? and more about operational excellence manager job. Get more data about operational excellence manager job for your career planning.
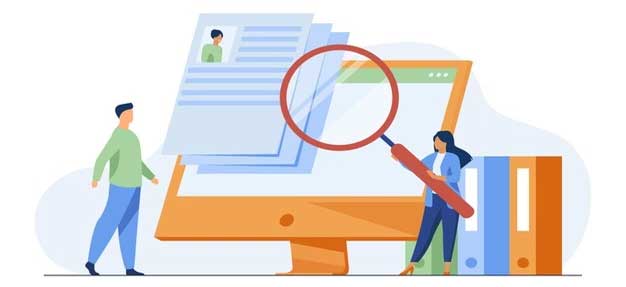
Operational Excellence
People are unsure of how to approach the subject of operational excellence. It is difficult to define and most people don't find the topic to be broad. Operational excellence is achieved when every member of the organization can see the value that is being put into the customer.
They should try to improve the value and delivery of it, even if they see it. Operational excellence is more than just about reducing costs. It is about creating a company culture that will allow you to produce valuable products and services for your customers and achieve long-term sustainable growth.
A nice story about Volunteer Manager career planning.
The Imprints of Operational Excellence on Business Process Improvement
The first step towards organizational excellence is to make it clear to all employees that the organization's systems are running smoothly and that team members can step in with improvements when necessary. Excellent companies manage their operations with the goal of delivering their product or service to the customer at the exact moment they want it, at the lowest cost, with the smallest effort, and at the price the customer wants to pay. Value streams are the processes for building products that your customers want.
The efficiency of value streams is the focus of the systematic improvements in operational excellence. The timing of value streams is visible. The assembly line is a value stream in a manufacturing plant.
Every process is running smoothly when the production rate is at its proper pace. When the rate is ideal, there are no problems with the flow of goods, there is no downtime, and there is a backup of semi-processed goods. Some experts think of operational excellence as a journey rather than a destination.
You can always get better, so your definition of excellence will change over time. Operational excellence is more than just bottom-line efficiency. It is about top-line growth.
The point of seamless flow is that you want management to be in the market. The Shingo Prize for Operational excellence was created in 1988 by Utah State University to recognize companies that excel in applying Shingo's principles. Insurers, military departments, pharmaceutical makers, and consumer products manufacturers have won before.
The Operations Excellence Manager at Silica
The Operations excellence manager is responsible for driving the excellence efforts within the U.S. Silica corporate and plant operations. The role is focused on improving the results of manufacturing and operational processes to improve efficiency, reduce cost and increase customer satisfaction. The VP of Operations will have the responsibility of the operations excellence manager.
Don't miss our story on Diversity & Inclusion Manager job planning.
What Do You Think About Operations Managers?
What do you think? How many of the top 10 qualities of an operations manager do you possess? Good for you if you think you have them all.
Operational Excellence in Healthcare
We will help you understand what operational excellence is. We will show you how other companies have achieved it, and how you can do it for yourself. We will help you through the process of hiring someone who can manage excellence.
Kevin J. Dugan defines operational excellence as a point where every employee can see the flow of value to the customer and fix it when the flow breaks down. Every employee is responsible for their tasks, so leaders of operationally excellent companies can shift their focus from managing day-to-day activities to continuous innovation and other activities to increase recurring revenue. Everyone in an organization knows their contribution to normal flow, can identify abnormal flow, and implement the standard methodology for correcting processes without management intervention.
Excellent visual systems are so simple that a visitor can look at them and see if they are on track without asking any questions, or looking at any computer printouts. Fuel for operational excellence is standard work. It is a standard procedure for every employee when an abnormality occurs.
The decision-making process is kept to a minimum thanks to standard work, and employees can repeat the process every time the flow of value is disrupted. When processes are excellent, you will meet the demands of customers without creating waste. Management will have time to research and find new ways to improve the product or create a new one.
Various industries have utilized operational excellence to build lean, predictable, andScalable processes that allow them to stay relevant and ahead of the competition. Improving processes to use resources more efficiently, eliminating mistakes and unnecessary procedures, and improving health outcomes are some of the things operational excellence in healthcare is focused on. MonteVista Homes has overcome its challenges since it decided to use a model called SweetProcess.
Read also our paper about Wealth Advisory Manager career description.
Operational Excellence in COVID-19
Since the COVID-19 pandemic began, operational excellence has become more important than ever for creating a resilient, adaptable organization. Since operational excellence is a data-driven approach where everything is constantly measured and assessed, investing time, money and employees in situations that don't result in a measurable outcome is a thing of the past. It takes a lot of effort by everyone at all levels of the organization to start the marathon.
Many operational processes exist because they have always been done that way, like that weekly 9AM Monday meeting where no one has anything to say, but no one is brave enough to stop showing up. A study found that 21% of managers, executives and directors ranked resistance to change as the main obstacle preventing the achievement of operational excellence. Lean is a system that maximizes value.
Lean is applicable to any industry and can be used to achieve operational excellence because it is focused on eliminating anything that doesn't add value. Although frequently used in manufacturing, Kaizen is also applicable to a lot of other places. The Japanese word for continuous improvement is called "kaizen", which was founded by Masaaki Imai over 30 years ago.









X Cancel