Plant Manager Job Description
Stewardship in the Plant, The Quality Control Manager of a Manufacturing Plant, Industrial Production Managers, The Plant Manager: A Key Accountable Person for the Operation of a Nuclear Reactor and more about plant manager job. Get more data about plant manager job for your career planning.
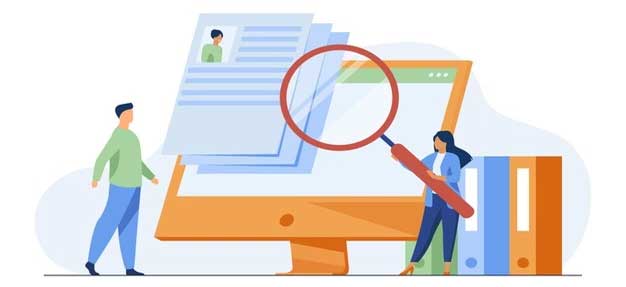
- Stewardship in the Plant
- The Quality Control Manager of a Manufacturing Plant
- Industrial Production Managers
- The Plant Manager: A Key Accountable Person for the Operation of a Nuclear Reactor
- Plant Managers
- Wind Site and Plant Managers
- A Plant Manager Position at School House Uniforms
- Plant Managers: What to Ask for in a Plant Management Position
Stewardship in the Plant
The plant manager will make sure policies and procedures are followed in all operations. They develop processes that maximize stewardship.
Don't miss our column about Fabrication Shop Manager job description.
The Quality Control Manager of a Manufacturing Plant
Plant managers are the people who organize and watch over the daily operations of a manufacturing plant. It is their responsibility to ensure the plant runs efficiently, quickly, safely, and smoothly. The plant manager will be in charge of all locations.
They monitor individual sections of the operation. Plant managers will assign workers, create work schedules, develop production schedules, and hire and train new staff to maintain optimal operation. They will collect and analyze new data to determine where waste could be occurring or where improvement could be made.
The plant manager is responsible for keeping an eye on worker safety, monitoring production equipment to ensure it remains in optimal working order, and repairing or replacing equipment as necessary. Quality control is the last line of defense for the plant manager. They keep in touch with other departments or sections of the plant to make sure operations are running smoothly.
Industrial Production Managers
Industrial production managers are in charge of a manufacturing facility. They are involved in the daily operations of the plant. They are usually responsible for the entire plant's operations at smaller plants.
Most plant managers have certain tasks that they are responsible for. Plant managers help with budget calculations. They compare expenditures to budget and adjust spending if necessary as the year progresses.
Plant managers can initiate or approve requests for capital purchases. They look at production rates and costs to see how well the plant is meeting standards. The plant manager is the most important person in most operations.
Plant managers might approve or request employee programs. Most employers prefer those with a four-year degree and relevant experience to become a plant manager. Industrial engineering and business administration are popular degrees for plant managers.
Large facilities might prefer candidates with graduate degrees. Newly hired plant managers often spend weeks in company-run training programs. Plant managers need the ability to motivate and train their personnel.
Detailed report on Associate Manager career planning.
The Plant Manager: A Key Accountable Person for the Operation of a Nuclear Reactor
A plant manager is in charge of the plant operation. Assures that the plant's production objectives are achieved at the lowest cost consistent with quality requirements while maintaining compliance to Federal, State, and Local Safety and Environmental regulations and laws. The delegates responsibility is to work with the key managers in production, production control, industrial engineering, cost accounting, maintenance, and other related operations to achieve the objectives set forth in the corporate business plan.
The Plant Manager wants to win and takes complete ownership of the plant operations. Through subordinates, supervisors and managers, the objectives of safety, quality, customer service, continuous improvement, cost, and production are met or exceeded. The team's performance is elevated by coaching and leadership in the areas of employee engagement, safety, quality, customer service, continuous improvement, cost, and equipment reliability.
Success depends on being able to build relationships with employees. The plant manager will be responsible for providing leadership and management. You will provide oversight for the day-to-day operations and proper functioning of the facility through hands-on leadership.
Plant Managers
You are expected to deal with a lot of finances as a plant manager. Financial management is one of the top skills a plant manager should have. They should be able to allocate the funds in a way that will allow them to use them as effectively as possible.
Being able to monitor their team's performance on a day-to-day basis one of the skills plant managers need to be successful. It will be possible to make necessary adjustments so that performance and productivity can continue to improve. Plant managers should take the time to ensure that their workers are doing the essential work, rather than allowing staff members to waste their time on less important things.
Sometimes a plant manager's team needs some extra motivation to get things done. A plant manager should help the team by lifting their spirits and making them feel better. Plant managers are faced with difficult decisions.
A plant manager needs to be able to assess a situation and come up with the best course of action. Plant managers need a system in place to review production processes. They should be familiar with the daily workings in their field.
Quality control checks are important to ensure the plant's success. Conflict can arise and come in many forms. A successful plant manager should be able to take control of any situation and find a solution to any conflict before serious issues arise.
Detailed story about Change Manager job description.
Wind Site and Plant Managers
The systems that generate and distribute electric power are controlled by the wind plant managers. They direct all wind plant operations. They are responsible for the smooth operation of wind plant activities and manage all wind plant employees, contractors, and equipment support teams.
The wind plant managers work with the Vice President of Operations, turbine service personnel, utility companies, and wind farm contractors to ensure the proper and safe operation of the facility. Wind site and plant managers have a lot of knowledge of wind turbine design, operation, system, subsystem, and component diagnosis and repair. They are familiar with the requirements for environmental safety and health in confined spaces, working at heights, chemicals and lubricants, and mechanical procedures.
A Plant Manager Position at School House Uniforms
Training for plant managers is done in lower-level positions. Plant managers begin as production workers and move up to supervisor positions before they reach the plant manager position. College graduates can move into a management position after completing an extensive management training program, as well as knowing company policies, production processes and safety regulations.
Management trainees may have to spend time in other departments before they are hired into a management position. Managers of plants must be able to give instructions to their employees. They must be able to read non-verbal signals, such as facial expressions, to understand how a message is being received.
They need to be able to give feedback. They can work well on a team but also act as a leader. Plant managers have compassionate skills.
They can stay on task by practicing self-control. A plant manager needs time-management skills such as the ability to set goals, prioritize tasks and create schedules. Plant managers need decision-making skills to make decisions.
They need to have self-motivation and focus because they work independently. Plant managers need to be organized to keep records and create an environment that facilitates the flow of information. Plant managers need leadership attributes such as motivation, self-esteem and confidence to be effective.
Don't miss our story about Quality Assurance Manager job description.
Plant Managers: What to Ask for in a Plant Management Position
A plant manager can help improve your business. How do you find the best talent for the position? Knowing what to ask will help you find out what skills and personality your plant manager has.
You can find questions to help assess a candidate's hard skills, behavioral intelligence, and soft skills. Accidents will happen in the workplace. Reducing them is one of the greatest challenges facing plant managers, it is necessary to reduce injuries, costs and downtime, because of accidents.
Plant managers are faced with another challenge, keeping important information safe from cyber theft or hacking. Every industry uses computers and smart plant managers make sure security measures are in place to protect sensitive data. Plant managers have a challenge in getting their staff to buy into the objectives and work together as a team.
Plant floor workers will often do things their way, focusing on their needs and objectives. Candidates should demonstrate the value of open communication. Plant managers are often called fire fighters because they solve the same problems over and over again.
Strong leaders will dig deeper to identify the root cause of the problem. They will try to put in place a system, procedure or practice that will eliminate the problem so it doesn't come up again. Operations often take the lead investigating customer satisfaction and reporting issues.









X Cancel