Process Operator Job Description
Process Operators: Anomaly Detection and Response, Degrees and Certification for Process Operator Position, Panorama: Identifying Process Owners, Six Sigma and the Vigilance of Process Owners and more about process operator job. Get more data about process operator job for your career planning.
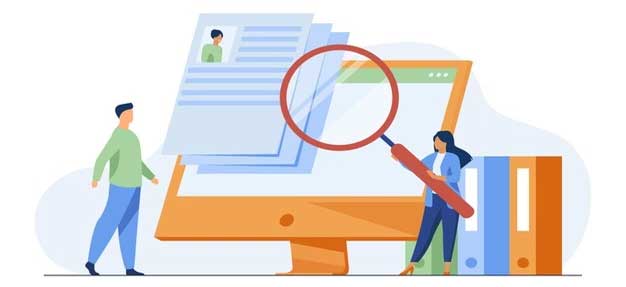
- Process Operators: Anomaly Detection and Response
- Degrees and Certification for Process Operator Position
- Panorama: Identifying Process Owners
- Six Sigma and the Vigilance of Process Owners
- The Operations Manager: A Generalized Business Analyst
- Process Technicians in Chemical Manufacturing
- Operation Management
- The Operations Manager of the GEORGETIC Company
- Process Operators in Chemical Plant
- Machine Operators
- The Skills and Qualities Required for a Machine Operator Job
- Business Process Managers
- Business Process Management: A Challenge for Organizations
- How to Make Your Operations Manual Easy
- Process Street: Documenting Business Processes
Process Operators: Anomaly Detection and Response
Process Operators are in charge of the full production process of a manufacturing plant. They monitor equipment to make sure it is working well. They are responsible for the safe operation, basic maintenance, and the problem of the facility's equipment and instruments.
Process Operators are skilled professionals who work as part of a team. The facility has a computer system that operates the machinery. They use the system to start the plant and shut it down.
See our study about Slitter Machine Operator job guide.
Degrees and Certification for Process Operator Position
A high school degree is required for working as a process operator. Degree requirements are not required in cases where the employers provide training. A bachelor's degree or technical certification is required for long-term goals such as salary raises and promotions. Process operators may be exposed to dust, noise, and chemicals at times, and may be at risk of dying at work.
Panorama: Identifying Process Owners
Can the company still function if the process owner is gone? There will be no one to monitor resolve issues when a process is still being executed. No process operates in a silo alone.
Process changes can disrupt systems and processes downstream. Process owners can help the company develop a change management plan that will ensure a smooth transition for affected employees. The consultants at Panorama can help you identify process owners and give them the tools and expertise to improve your processes and competitive advantage.
A good column on Dish Machine Operator job planning.
Six Sigma and the Vigilance of Process Owners
All good. Those people have earned their Six sigma status. One can find process owners who are doing an exceptional job if one examines closely the companies which are sustaining the gains from Lean Six sigma efforts.
7. Provides linkage to other processes. A process owner is the link between a process and the rest of the world.
The process owner needs to maintain connections in all directions, even if they are not working on the process. There are 8. It's important that process operators have the training and resources to do their jobs.
A good process owner is a good servant to the process operators. It is the operator's job to figure out what they need in order to do their job well and keep getting better. Appropriate training, materials and information are included in those needs.
There is no glamour to the process of ownership. The work is routine. Process owners play a critical role in determining whether a company's processes hum along or fail.
The Operations Manager: A Generalized Business Analyst
Operations management is a field of business that deals with the administration of business practices to maximize efficiency. It involves planning, organizing, and overseeing the organization's processes to balance revenues and costs and achieve the highest possible operating profit. An operations manager is tasked with ensuring that the organization successfully converts inputs into outputs in an efficient manner.
Product design is the process of creating a product that will be sold. It involves generating new ideas or expanding on current ideas in a process that will lead to the production of new products. The operations manager is responsible for ensuring that the products sold to consumers meet their needs and match current market trends.
The operations manager manages the supply chain process by controlling inventory, production, distribution, sales, and suppliers to supply required goods at reasonable prices. A properly managed supply chain process will result in an efficient production process, low overhead costs, and timely delivery of products to consumers. The operations manager can focus on different projects without getting distracted by the many processes.
The operations manager should be able to plan, execute, and monitor each project. If a manager is disorganized, tasks will pile up, important documents will get lost, and a lot of time will be spent looking for lost documents that could be easily accessible. Good organization skills can help the manager.
See our paper on Process Analyst job guide.
Process Technicians in Chemical Manufacturing
The role of a process technician is broad. Process technicians are responsible for monitoring and improving manufacturing processes. They are employed in a wide range of industries.
Process Technicians are employed in any industry that converts raw materials into resources. Process Technicians have different responsibilities in different industries. Process technicians have to understand the equipment they are responsible for.
Process Technicians must know the right settings for each piece of equipment. They are responsible for making sure equipment is in good working order. Process technicians have to be very careful.
They are responsible for keeping equipment and areas clean. Process technicians in bio-manufacturing have to clean their workplace. One has to follow standard operating procedures in a sterile environment as the environment can ruin an entire batches of chemicals.
Maintenance logbooks are one of the responsibilities of process technicians. They are responsible for keeping test logs. Process technicians use a blend of soft skills and technical knowledge to complete their jobs.
Operation Management
The direction and control of the process that transforms inputs into products and services is referred to as operation management. Operations management underlies all functional areas because processes are found in all business activities. The operation refers to a department.
See also our report on Mortgage Processor job guide.
The Operations Manager of the GEORGETIC Company
The Operations Department has established and set up the management of labor, productivity, quality control, and safety measures. The operations manager will make sure operations are safe. As a company representative, you will be involved in regulatory issues.
Process Operators in Chemical Plant
Process operators are responsible for overseeing the production process of a chemical plant facility. The goal of a process operator is to make the manufacturing plant more efficient and safe.
A nice story on Owner Operator career guide.
Machine Operators
Machine operators can use computer-operated equipment or mechanical equipment. They install their machines, operate them, and perform maintenance checks. They are team players who like to work on computers and mechanics.
Machine operators install, maintain, and operate machines. They need to have a good understanding of machines. In order to prepare a machine operator for their job, in-depth training is required.
Machine operators can work with machines. They must be able to use machinery and tools. Machine operators must be able to find solutions to machinery problems.
The Skills and Qualities Required for a Machine Operator Job
A machine operator is a person who is trained in operating, controlling, and maintaining high speed sophisticated machines and equipment that are used in the manufacturing of smaller production equipment and other utility products. Machine operators perform a number of duties, which include arranging and testing machines before production, cleaning up machine parts after each work procedure, and fixing machine problems. 2.
There is attention to detail. The work of a machine operator is delicate and requires attention. Failure to concentrate can lead to unnecessary mistakes.
3. Communication skills are important. The machine operating job requires that the operators work on a team with their supervisors and coworkers.
The operator must be able to listen and follow instructions with little supervision. They need the ability to write well. 5.
There are machine limits and capabilities skills. Machine operators should be able to choose the most efficient machine to work with. They need to understand the limits of the machines they are expected to operate and coordinate several machines working together.
See also our article on Store Operator job guide.
Business Process Managers
To be good on your job as a business process manager, or to increase your chances of being hired for the role, you must have a sound educational background and training. Business process managers are expected to be good at leading others because they are in charge of the team. Superb organization and coordination ability is important to your success and that of the team. Having an excellent business sense is a very important trait of a business process manager.
Business Process Management: A Challenge for Organizations
Businesses rely on processes to manage their daily tasks. Some processes are large and complex while others are small and simple. There are processes for hiring and firing, those to help create and stay within budgets, and those for interacting with customers and employees.
The approach of the BPM is to improve processes throughout the organization. Professionals who acquire and develop knowledge and skills in business process management can help add value to the organization. Business operations are changing and becoming more complicated, making business process management a high priority.
Read also our paper on Retail Operator career planning.
How to Make Your Operations Manual Easy
The only way to prevent errors is to document processes and workflows, and the only way to make sure employees know how to do it is to create a manual. The consistency of your business is the main reason why processes are important. By having a method that can be executed perfectly time after time, you can make it easy to find problems and deal with them.
You could document your processes, hierarchy, job descriptions, emergency procedures, and more without a manual. They only turn from random files into a coherent document when they are collected in a single location. As your company grows, your documented processes will be the largest section of the operations manual.
The trick is to make it easy to follow. You need to choose how you want to create your manual. There are a couple of problems with using a word processor to create and print physical copies and then store them in a file.
If you print out a manual, you will have to either add an appendix or completely rewrite it. If you use an appendix, it will make it difficult to use your manual because you are giving your employees a convoluted mess of addendums to use. Having your processes in a central location means that you can access them whenever you have an internet connection.
If you want to have a physical copy of your processes, you can also print them out from Process Street, which will eliminate the advantage of a program like Word. The details you need to sort out are simple, such as the type of text you use, how you separate each section, and so on. If you use Process Street, you can organize your processes into subfolders by creating a folder.
Process Street: Documenting Business Processes
Let's discuss process documentation Writing down your business processes is one of the things that process documentation does. Documenting business processes can help employees know what they have to do, how they should do it, and how to complete recurring tasks efficiently and effectively.
The operations manual has process documentation at the center. It is never an SMB's vision to stay small. People working at the company want to become well-known and well-regarded, and that is usually what they want.
The process of growing in size and stature can be a downfall for many businesses. The nightmare of scaling can be a dream if you have a company operations manual. It is easier to train new hires, provide long-term employees with the right information, and have a referencable silo of processes and procedures with an operations manual.
The Contentwidget is on the right-hand side of the editing screen and can be used to add more text, images, or subchecklists. There is a button in the bottom left-hand corner of the editing screen that you can use to add more procedures. You are keeping organized even though you are using Process Street to create processes.
It could take employees a while to find the processes they are looking for. If you document your processes and procedures as templates, you can use them to launch an infinite number of checklists to help you do stellar work. Every.









X Cancel