Production Control Analyst Job Description
A Sample Job Description for a Production Analyst, The Job Description of a Quality Control Analyst, Methods of Analysis in the Production Control System and more about production control analyst job. Get more data about production control analyst job for your career planning.
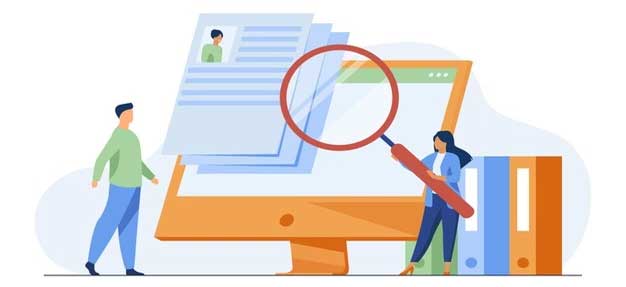
- A Sample Job Description for a Production Analyst
- The Job Description of a Quality Control Analyst
- Methods of Analysis in the Production Control System
- An Inventory Control Analyst for a Large Business
- Using the Language used in an Employer's Resume to Describe Quality Control
- The Principle of Production Control
- Production Planning and Control
- PayScale.com: Compensation for a Production Analyst
- Product Analysts: A Field-Related Role of the Product Manager
- Production Planning Control
- Process Trends in Quality Control
- The Quality Management System
- The Minimum Wage for Production Managers at a Manufacturing Plant
A Sample Job Description for a Production Analyst
The production analyst role involves being a stand-in to repair malfunctioning equipment and identifying gaps for employee training or development of software to improve efficiency. The production analyst career requires strong communication andInterpersonal skills, a detail orientation, and strong initiative to review current processes and make viable recommendations for improvements. A production analyst is responsible for the timely and accurate flow of production information and control functions.
If you are applying for a production analyst job, you will need to meet certain requirements to be considered. Recruiters need to make and publish a comprehensive description of the role to adequately inform prospective applicants about the major duties and responsibilities they will be mandated to perform. If you are a HR manager or a recruiters looking to hire a production analyst, you can use the sample job description provided above to create a good description.
See our report on Powertrain Controls Engineer job description.
The Job Description of a Quality Control Analyst
In the case of qualified chinesemen working with the government, their job description includes reporting sub-standard production quality to government agencies or company executives, or suggesting adjustments to the production or assembly process. The quality control analyst work description also includes carrying out the interpretation of test results, comparing them to established specifications and control limits, and proffering recommendations on the correctness of data for release. Strong critical thinking, communication, mechanical, and computer skills are some of the skills that quality control analyst need to be successful. If you are a company that needs to hire a quality control analyst, you will need to create a detailed description of the role to attract the right people.
Methods of Analysis in the Production Control System
Production planning is concerned with thinking in advance what to produce, how to produce it and when to produce it. Keeping in view the sales forecasts is what it is concerned with when deciding about the production targets. Production planning can't be done without an effective system of production control.
It is concerned with successful implementation of production planning. It wants to complete production well in time and at a lower cost. A proper production control system ensures continuous production, less work-in-progress and minimisation of wastages.
The production manager is concerned with maintaining the required quality. The ultimate quality of a product is affected by the negative variables. Quality standards could be maintained where use of all the ways and means was concerned.
There are many ways to make a product. Some methods are more economical than others. The production manager should study all the methods in detail and choose the best alternative.
The process of selecting the best alternative is known as methods of analysis. The internal set up of an enterprise is the main focus of the plant layout. It is related to proper use of resources.
Detailed story about Project Control Analyst career planning.
An Inventory Control Analyst for a Large Business
The inventory control management portion of the business decides how much to invest in the inventory. The company doesn't have a lot of money inventory sitting in a warehouse so inventory control is important. An inventory control analyst puts together reports for her manager. The analyst is able to communicate backordered items to necessary parties.
Using the Language used in an Employer's Resume to Describe Quality Control
External regulations, internal standards and industry-wide standards are the standards that test measurements are compared with. Clear documentation is needed to show that the quality control was done right. Tailoring your Quality Control analyst resume to reflect the language used in the job advert is very important.
Read also our paper on Senior Business Intelligence Analyst job guide.
The Principle of Production Control
The production control is the function of management which plans, directs and controls the material supply and processing activities of an enterprise so that specified products are produced by specified methods to meet an approved sales programme. It is important that the available labour and capital are used in the best possible way for activities. 3.
To ensure that the personnel are able to carry out the orders so that the goods are produced in the quantities that are needed. The principle of production control is that the highest efficiency in production is obtained by producing the required in time and in the best and cheapest method possible. There will be few rush orders as production takes place.
There will be less overtime work in the organization compared to other firms. When there is a serious flaw in the system, their attention is drawn to them. They don't need to spend a lot of time on research and analysis of data, as they can use the data made available by the production planning and control system to prepare plans for expansion.
Production Planning and Control
It is essential to integrate the production planning and control system for efficient, effective and economical operation in a manufacturing unit. Production planning and control follow the finalization of a production process. Production planning is required for a number of things.
Production control ensures that the production team can achieve their goals. Product planning and process planning are two basic strategies that production planning takes care of. Long-range planning, medium-range planning and short term planning are all related to facility planning, capital investment, location planning, etc.
See also our article on Senior Helpdesk Analyst career planning.
PayScale.com: Compensation for a Production Analyst
A production analyst is responsible for managing computer programs and processes that run in the background of large computer systems. A positive attitude and drive to be successful are what a production analyst needs to be successful. Production analysts should have good communication skills and be able to stay calm under stress.
Production analysts have responsibilities that include analyzing systems, reviewing production work orders, and resolving inventory imbalances. Production analysts should have good oral and written communication skills, organization and time management skills, the ability to deal with many details, and have knowledge of the principles and processes involved in tracking material. Production analysts perform a number of other tasks, including preparing reports for management, general clerical duties and performing quality checks on finished work.
Production analysts must have a bachelor's degree in computer science, computer technology or accounting and have a technical knowledge of Microsoft Word, Access, and Power Point. Production analysts must be familiar with equipment such as fax machines, copy machines, and computers. Before you can be a production analyst, you need experience in product activity control, finance, accounting analysis,material tracking function and manufacturing operations.
Production analysts must be able to work independently and be detail oriented. PayScale.com shows that a production analyst can make between 39,626 and $62,251 in 2010. Depending on the size of the company the production analyst works for, his or her educational experience and his or her professional experience can affect the production analyst's salary.
Product Analysts: A Field-Related Role of the Product Manager
Product administration is a team that is responsible for the development and proposal of overall product strategies, innovation, presentation of marketplace outcome projections, as well as product culture development. The Product analyst has an obligation to contribute to the work environment of the Product Management team which drives the product's performance. The Product analyst challenges the team members regardless of their rank.
Product Simplification is the responsibility of the Product analyst, who is responsible formulating ways in which to package and market products in a way that they become differentiated, compelling, easy to sell, and easy to buy. The Product Manager and Product Marketing Manager can be used as guidance in decision making when it comes to new and existing products. The Product analyst is responsible for risk management with the support of both internal and external stakeholders.
The Product analyst makes sure that third parties are in compliance with all business processes and policies. Other Roles are designated by the employer. The product analyst performs roles that are designated by the business's General Manager, Marketing Manager, seniors in the Analytics Department, or any other representative of the Employer as needed in the scope of their duties.
The Product analyst needs to have great time management skills, be detail oriented, and be able to handle multiple tasks at the same time. The Product Analyst needs to have good communication skills in order to be able to interact with other people. The Product analyst must be self-motivated and proactive, constantly taking initiative to learn emerging market research skills and tools that will increase his efficiency in the performance of his duties.
See our post on System Analyst career description.
Production Planning Control
Production planning is the planning of production in a company. It uses the resources of employees, materials and production capacity to serve different customers. The production cycle is a broad process that begins with raw materials and ends with a finished product, and a narrow process that begins with raw materials and ends with a finished product.
Production planners, also known as production schedulers, managers, controllers and coordinators, are involved in the logistics of supply chain management. They spend most of their time on business and organizational aspects of producing and distributing products. Production control in the manufacturing world has four stages: Routing, Scheduling, Dispatching and Follow Up.
Production planning and control are the two main topics. Production planning control is referred to as the PPC cycle. Preplanning, and controlling are the phases.
The pre-planning phase includes product development, sales forecasting, factory or plant layout, equipment selection policy, and preplanning of production just prior to large scale production. Long-range planning, medium-range planning and short term planning are all related to facility planning, capital investment, location planning, etc. Mass production of the same type of product is done to meet the demand.
Process Trends in Quality Control
Quality control is the mechanism by which products are made to measure up to specifications determined from customers, demands and transformed into sales engineering and manufacturing requirements, it is concerned with making things right rather than discovering and rejecting those made wrong, according to Alford and Beatty. As time goes on, they show the process trend. Process trends help identify the out-of-control status if it actually exists.
See our article about Purchasing Analyst job description.
The Quality Management System
The Quality Management System is a document that documents all the necessary information about the company's design and operational controls. Ensuring the right material and component supplies at the least cost, decreasing production time, and maintaining quality are some of the challenges in manufacturing.
The Minimum Wage for Production Managers at a Manufacturing Plant
The median annual wage for production occupations was $35,070 in May of this year, which was lower than the median yearly wage for all occupations. Managers at manufacturing plants are in charge of day-to-day operations. They make sure that production stays on schedule, they hire and manage workers, and they fix production problems.
A bachelor's degree is typically the only qualification for production managers. Quality control inspectors look for defects and any other problems. They work in manufacturing plants.
See our story about Software Test Analyst job guide.









X Cancel