Quality Control Job Description
QC Technicians, The quality of laboratory reagents, solutions and reference media, Quality Control Inspectors, The role of the personnel in ensuring that test results meet specification and more about quality control job. Get more data about quality control job for your career planning.
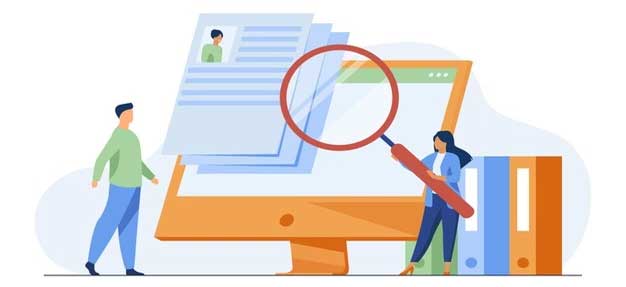
- QC Technicians
- The quality of laboratory reagents, solutions and reference media
- Quality Control Inspectors
- The role of the personnel in ensuring that test results meet specification
- Quality Control and Monitoring
- Quality Control in a Large Organization
- Qualifications of a Quality Control Officer
- Quality Control Managers
- How to Write a Resume for Quality Control Inspector
- ISO Standards for Quality Control
QC Technicians
There are different sectors where QC technicians can be found. They help to set up and manage quality control systems. Quality control technicians have to be fit because they have to be fit most of the time and also check on things to make sure everything is going well.
See also our post on Plant Controller job planning.
The quality of laboratory reagents, solutions and reference media
The results should be recorded. The results of parameters that are identified as quality attribute should be trended and checked to make sure they are consistent with each other. Any calculations should be looked at with suspicion.
The quality of laboratory reagents, solutions, glassware, reference standards and culture media should be given special attention. They should be prepared and controlled. The level of controls should be adjusted to the data available.
Animals used for testing should be kept away from each other. They should be kept in a way that assures their suitability for the intended use. They should be identified and records should be maintained.
Quality Control Inspectors
If a product fails to meet the quality standards, it will affect the business sales and customer satisfaction levels. Ensuring that your organization has a good quality process is important. The work process is smooth with the hiring of a quality control inspector.
A quality control inspector is hired to watch for quality issues incoming raw materials and products that are ready to be shipped. They make sure that manufactured products meet the quality standards set by the organization before being sent to customers. The quality control inspector job role involves analyzing the data and conducting tests.
They are engaged in a lot of different things, from food to electronics to automobiles. They sort out the items that don't meet the quality standards and improve the production process to reduce the chances of failure. The quality control inspectors should have a good knowledge of the types of equipment and computer programs used in the organization.
They must know technical documents and blueprints to make sure products meet quality standards. The quality control inspectors may need to train their employees. They must be able to teach employees how to prevent flaws and work towards a smooth process.
A quality control inspector should be aware of the differences in products to meet the standards. They must be aware of the changes. Quality Control Inspectors can progress in the field as a trainer, team leader, and supervisor with experience.
Detailed study about Document Control Specialist career planning.
The role of the personnel in ensuring that test results meet specification
The purpose in the end is the same despite the different roles. The test results must meet the acceptance criteria established by the specification and be reliable because the procedures used were in line with the standard. There will be less opportunity for non-conformities, resulting in lower costs and on-time delivery, if roles and responsibilities of the personnel are understood. The owner will have a quality product that maximizes the asset's service life at reduced overall costs, while the contractor will keep their reputation for providing quality work that helps ensure a continuous revenue stream.
Quality Control and Monitoring
The QU is given authority to create, monitor, and implement a quality system. The daily responsibility of manufacturing personnel to build quality into the product is not replaced by activities. The QU should not take on the responsibilities of other units of the manufacturer.
The product and process development units, manufacturing units, and the QU are expected to remain independent under a quality system. A single individual can perform both production and quality functions. The person is still responsible for implementing all the controls and reviewing the results of manufacture to make sure that the product quality standards have been met.
Detailed column about Control Panel Technician career description.
Quality Control in a Large Organization
Quality control is a huge responsibility. Quality control executives are the ones who make sure the quality of the work is good. Sometimes a group of people are hired to make sure the work is going according to the plans.
Ensuring that the quality of the products and services remain the same throughout the company is one of the responsibilities of quality control. Quality control executives should be able to restore it if there is slack in them. Quality control is one of the major responsibilities and it involves inspecting the various departments for compliance with rules and standards.
The selection of raw materials, the beginning of the making process, through the packaging department to printing content on the items are some of the stages where checking takes place. It is mandatory to follow the laws in the industry. The state or central government gives an identity to the company with the certification and grading.
It adds to their brand value and is considered a grade by a trusted authority. Quality control executives are required to be in touch with employees to make sure they understand the standards of working well and remain accessible for consultation. They have a responsibility to see to it that the management policies and important certifications are followed.
Qualifications of a Quality Control Officer
A quality control officer needs a certain set of skills and abilities to help him carry out the tasks assigned to him as part of his position in the organization. A quality control officer needs to have certain qualifications in order to perform the tasks that are assigned to him in his job role. A quality control officer is a professional who is responsible for ensuring that all the products that are manufactured in the industry are in line with the legal regulations and customer requirements.
The Quality Control Officer is a highly focused job that conducts special operations and programs to ensure the quality standards by maintaining the reliability of products. Quality Control Officers are referred to as QC testers. They are involved in measuring the existing goods and services against the previous ones in order to produce better services for the customers.
Don't miss our column about Pest Control Technician career guide.
Quality Control Managers
Quality Control Managers with advanced degrees can be promoted easily. They can become an independent consultant. Many organizations need experienced professionals to improve production quality, reliability, and reduce production costs.
Quality Control Managers are not responsible for monitoring the quality of the products but are responsible for monitoring whether the products are necessary for the production process. They work with other departments to make sure the product met the desired standards. To be a quality control manager, they have to regularly upskill and reskill by taking up industry-recognized quality management training programs to coordinate with other quality management professionals.
How to Write a Resume for Quality Control Inspector
A quality control specialist with over two years of experience has a detail-oriented quality control philosophy. New guidelines cut inspection time by 30%. Seeking to become the next supervisor at Queens Industrial.
A quality control inspector is a management level employee who oversees the quality checking process, the safety of manufactured products, or the readiness of software, in addition to supervising the tasks of other QC employees. How to write a resume with no experience in quality control? It is the same thing.
When writing your work history entries, think about the most relevant bullet points from the QC. There is no way to quantify soft skills, but the hiring managers know that every candidate adds them. The quality control resume should include the hard skills they ask for in the job description.
Read our article on Production Control Specialist career guide.
Quality control inspectors may work with other people. Sales or account managers may communicate with the inspector to pass on concerns from a client that need to be addressed in the production process. The number of quality control inspector posts has fallen as more sophisticated equipment is used to pick up inconsistencies. Workers are now required to take full responsibility for the quality of their own output so that the inspection activities can be reduced.
ISO Standards for Quality Control
Quality control is about making sure the products are of high quality. The lower cost to customers could be provided by the company. It is important that all the plans are implemented and goals are met.
There are several ISO standards that should be met when releasing products. Quality management, auditing, environmental management, and risk management are some of the characteristics that are included in ISO standards. Reliability, efficiency, and maintainability are some of the ISO standards for quality control.
See our post about Quality Engineer career description.









X Cancel