Quality Control Supervisor Job Description
A Qualification for a Quality Control Supervisor, The Job Outlook of Quality Supervisors, The Quality Control Manager at a Linear Plant and more about quality control supervisor job. Get more data about quality control supervisor job for your career planning.
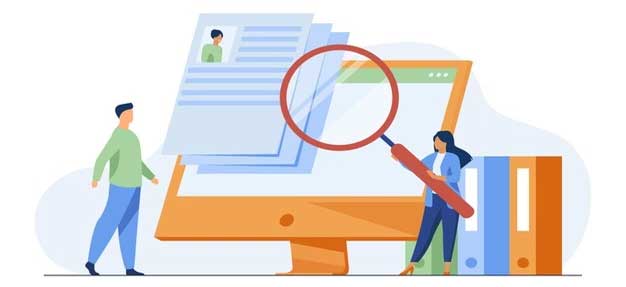
A Qualification for a Quality Control Supervisor
A high school degree is required to become a quality control supervisor. Education requirements may be different depending on the company and product being inspected. Good math and communications skills are required.
Knowledge in machine operation, assembly, and other industry-specific procedures, as well as training in the use of tools such as computers, meters, and gauges is usually needed. A quality control supervisor should have a good understanding of the various production needs, safety requirements, and processes of a company. It is a way to make sure that safety procedures are followed.
If a quality inspection is taking place at a plant that packages food products, you would expect the production staff to wear hairnets and gloves. A quality control supervisor makes about $70,000. Quality assurance jobs require an attention to detail because faulty products can cause a company millions in product liability lawsuits.
Read also our paper on Quality Assurance Manager job description.
The Job Outlook of Quality Supervisors
Quality supervisors want the customer to be happy with the finished product. The quality supervisor is responsible for communicating with the customer clearly and setting realistic expectations for when the issue will be solved. Quality supervisors report on metrics to other people.
Everything is executed to the highest possible standards in the operations of the organization. Most companies require a minimum of an associate's degree for applicants with a high school diploma or GED. A bachelor of science degree is more attractive for hire than a few years of experience in quality control.
The Quality Control Manager at a Linear Plant
The Quality Control Manager is an important part of the team and helps define and carry out appropriate tests and inspections to confirm a product complies with quality standards. The job of inspecting incoming materials and documenting test results is important. The Quality Control Manager is responsible for ensuring that the plant follows and complies with quality protocols.
The Quality Control Manager is responsible for the management of quality technicians. Responsibilities include cost efficiency, continuous improvement on processes, service, and safety for an entire business unit across all shifts. The Quality Control Manager works with production, maintenance and warehouse teams to communicate quality procedures and develop sustainable practices to maintain superior quality process.
Quality Control Manager is responsible for inspecting all products and determining what is acceptable and what is not. Products that are acceptable are released to inventory or rejected. The quality management program is overseen by the Quality Control Manager.
See also our report on Quality Service Representative job planning.
Quality Control Managers
Quality Control Managers with advanced degrees can be promoted easily. They can become an independent consultant. Many organizations need experienced professionals to improve production quality, reliability, and reduce production costs.
Quality Control Managers are not responsible for monitoring the quality of the products but are responsible for monitoring whether the products are necessary for the production process. They work with other departments to make sure the product met the desired standards. To be a quality control manager, they have to regularly upskill and reskill by taking up industry-recognized quality management training programs to coordinate with other quality management professionals.
How to Write a Resume for Quality Control Inspector
A quality control specialist with over two years of experience has a detail-oriented quality control philosophy. New guidelines cut inspection time by 30%. Seeking to become the next supervisor at Queens Industrial.
A quality control inspector is a management level employee who oversees the quality checking process, the safety of manufactured products, or the readiness of software, in addition to supervising the tasks of other QC employees. How to write a resume with no experience in quality control? It is the same thing.
When writing your work history entries, think about the most relevant bullet points from the QC. There is no way to quantify soft skills, but the hiring managers know that every candidate adds them. The quality control resume should include the hard skills they ask for in the job description.
A good column on Travel Consultant Supervisor career description.
Supervision Skills Questionnaire
Communication skills are important for a good supervisor. They need to communicate important information to their staff. Supervisors should strive to keep an open door for employees to approach them with their needs or issues.
The supervisor should be an example to their staff. They must make their employees want to follow them as they take their organization through normal business changes. A strong leader will encourage their team.
There are some tasks that a supervisor needs to deal with that require good critical thinking skills. There are more responsibilities and decisions to be made in a high-level position. Critical thinking skills make the decision process simpler.
Time management is important in a business. Being able to juggle timelines and meet goals regularly means supervisors must have both the awareness of when things need to be completed and how long it takes to do them. Supervisors should use their skills to deal with issues in the workplace.
A manager can use great problem solving skills to assess the situation and develop a plan to tackle it. The overall work of their employees needs to be directed by their supervisors. Their view of work is different than that of their employees.
Time Management for Software Quality
Managing your time well will ensure you have enough time to complete your tasks and confirm they comply with specifications. It reduces stress and makes it easier to complete your duties. When you meet your deadlines, you also make sure others who rely on you have enough time to meet their own deadlines without affecting their work quality.
Problem-solving skills can help you find solutions if you are struggling to meet quality standards. When challenges arise in your duties, a combination of creativity, logic and critical thinking can serve you. Communication skills that are strong can help you explain how to improve processes to other people.
Your listening skills are important for understanding what your colleagues need from you. Strong written communication is a must for software testing and other quality assurance roles. Quality assurance requires understanding quality standards.
Employees are expected to work within the company's standards. Understanding the guidelines set by the Food and Drug Administration can help you meet quality expectations. Supplemental training can teach you new practices and remind you of some techniques you may have overlooked.
See our paper on Field Operations Supervisor job planning.









X Cancel