Quality Control Technician Job Description
QC Technicians, Quality Control Technicians, A Qualification Test for a Quality Technician, Quality Control Inspectors, The Project Manager - A Technician and more about quality control technician job. Get more data about quality control technician job for your career planning.
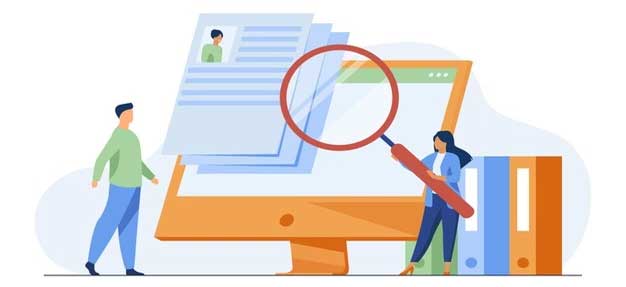
- QC Technicians
- Quality Control Technicians
- A Qualification Test for a Quality Technician
- Quality Control Inspectors
- The Project Manager - A Technician
- The role of the personnel in ensuring that test results meet specification
- Preparing for a Quality Control Interview
- How to Write a Resume for Quality Control Inspector
- The Role of Humans in Quality Assurance
- Time Management for Software Quality
- Apprenticeships in Quality Control
- Preparing for an Interview
QC Technicians
There are different sectors where QC technicians can be found. They help to set up and manage quality control systems. Quality control technicians have to be fit because they have to be fit most of the time and also check on things to make sure everything is going well.
See our article on Kitchen Equipment Service Technician career description.
Quality Control Technicians
Quality control technicians are part of the manufacturing team. Quality control technicians make sure that the products being made in their factory meet the criteria outlined by management. Quality assurance is part of the overall quality management process and helps to ensure that quality requirements are fulfilled as outlined in the ISO 9000 Standards.
Quality control is only part of the quality management process. Quality assurance is the assurance to both customers and the company that a product is of the highest caliber. Quality control is related to the process.
Quality control officers are required to read blueprints and specifications of the products they are creating. They need to be familiar with the entire process. They should be aware of the roles of each person in the production process.
Quality control officers look at operations to make sure they meet the standards. They recommend that the process be adjusted to make sure the quality is maintained. Quality control technicians inspect, measure, and evaluate products as they are produced to make sure they are of adequate quality.
Quality control technicians are tasked with rejecting finished items at the end of the production process. The items that do not meet specifications are removed from the output. The product may be examined further to see if it can be improved.
A Qualification Test for a Quality Technician
Quality control technicians are junior level employees who perform quality control checks on company products to ensure they meet required safety and quality standards. Quality technicians need a keen eye for detail and the ability to focus for long periods, but they are provided with on-the-job training. To be a quality technician, you need to have a strong working knowledge of mathematical concepts, excellent visual awareness, and the ability to work with minimal supervision. A top-class quality technician can efficiently monitor the integrity and quality of products without affecting production rates.
Read our article about Solder Technician job description.
Quality Control Inspectors
If a product fails to meet the quality standards, it will affect the business sales and customer satisfaction levels. Ensuring that your organization has a good quality process is important. The work process is smooth with the hiring of a quality control inspector.
A quality control inspector is hired to watch for quality issues incoming raw materials and products that are ready to be shipped. They make sure that manufactured products meet the quality standards set by the organization before being sent to customers. The quality control inspector job role involves analyzing the data and conducting tests.
They are engaged in a lot of different things, from food to electronics to automobiles. They sort out the items that don't meet the quality standards and improve the production process to reduce the chances of failure. The quality control inspectors should have a good knowledge of the types of equipment and computer programs used in the organization.
They must know technical documents and blueprints to make sure products meet quality standards. The quality control inspectors may need to train their employees. They must be able to teach employees how to prevent flaws and work towards a smooth process.
A quality control inspector should be aware of the differences in products to meet the standards. They must be aware of the changes. Quality Control Inspectors can progress in the field as a trainer, team leader, and supervisor with experience.
The Project Manager - A Technician
The work description for a technician includes performing site audits of suppliers production and processes to ensure compliance with necessary requirements, assisting the engineer and the director of quality in relating with vendors to conduct test runs, and providing solution to problems, monitor and follow up with quality assurance management.
See our post about Environmental Field Technician job description.
The role of the personnel in ensuring that test results meet specification
The purpose in the end is the same despite the different roles. The test results must meet the acceptance criteria established by the specification and be reliable because the procedures used were in line with the standard. There will be less opportunity for non-conformities, resulting in lower costs and on-time delivery, if roles and responsibilities of the personnel are understood. The owner will have a quality product that maximizes the asset's service life at reduced overall costs, while the contractor will keep their reputation for providing quality work that helps ensure a continuous revenue stream.
Preparing for a Quality Control Interview
Quality control has many jobs and roles, including Quality Control Inspector, Manager, analyst, and Administrator. All of which require exceptional communication, attention to detail, and the ability to work towards strict deadlines. Before you start preparing for a Quality Control interview, you should read the job description and create some examples of what you can do in the role.
A good post on Material Control Specialist job description.
How to Write a Resume for Quality Control Inspector
A quality control specialist with over two years of experience has a detail-oriented quality control philosophy. New guidelines cut inspection time by 30%. Seeking to become the next supervisor at Queens Industrial.
A quality control inspector is a management level employee who oversees the quality checking process, the safety of manufactured products, or the readiness of software, in addition to supervising the tasks of other QC employees. How to write a resume with no experience in quality control? It is the same thing.
When writing your work history entries, think about the most relevant bullet points from the QC. There is no way to quantify soft skills, but the hiring managers know that every candidate adds them. The quality control resume should include the hard skills they ask for in the job description.
The Role of Humans in Quality Assurance
If you work in quality assurance, you know how quickly emerging technologies are changing the nature of your work. The internet of things, machine learning, andRFID tracking are just a few of the new disruptive technologies that are almost certainly going to impact your career in one form or another in a few years. Quality assurance is about preventing a bad product from being produced and keeping it from reaching the consumer so that it can do harm.
Quality assurance workers who demonstrate an ability to understand interpret data have an advantage over those who don't. Those who can take the data, boil it down, and use it to communicate with other people have the greatest advantage. Quality assurance processes and protocols can be implemented with project management skills.
When a company makes significant changes to their processes, project management can affect the quality of the process. Implementing any of the technologies poised to impact the work done by quality assurance teams will be no easy feat. Incorporating them in the supply chain will require a solid foundation in project management and a good understanding of both the QA process and the supply chain.
Quality assurance workers should develop specific industry expertise to increase their job security as more of the job is automated through the use of technology. Being effective in quality assurance requires an understanding of how the product affects humans. It requires a sense of what is at stake if bad product leaves a facility.
It requires a level of compassion for the end users. Big Data, machines, and robots are tools. Quality assurance processes will be helped by them.
See also our column on Quality Assurance Analyst career description.
Time Management for Software Quality
Managing your time well will ensure you have enough time to complete your tasks and confirm they comply with specifications. It reduces stress and makes it easier to complete your duties. When you meet your deadlines, you also make sure others who rely on you have enough time to meet their own deadlines without affecting their work quality.
Problem-solving skills can help you find solutions if you are struggling to meet quality standards. When challenges arise in your duties, a combination of creativity, logic and critical thinking can serve you. Communication skills that are strong can help you explain how to improve processes to other people.
Your listening skills are important for understanding what your colleagues need from you. Strong written communication is a must for software testing and other quality assurance roles. Quality assurance requires understanding quality standards.
Employees are expected to work within the company's standards. Understanding the guidelines set by the Food and Drug Administration can help you meet quality expectations. Supplemental training can teach you new practices and remind you of some techniques you may have overlooked.
Apprenticeships in Quality Control
Quality control technicians are responsible for checking that industrial products and processes meet national and international quality standards. You can train as an apprenticeship in your chosen industry and then work your way up to a quality control position. Depending on the local jobs market and skills employers need from their workers, the range of apprenticeships in your area will be different.
Don't miss our article on Information Systems Technician career guide.
Quality control technicians are responsible for checking that products and services meet required quality and safety standards. They work in a wide range of industries.
Preparing for an Interview
You can maintain control by preparing early. You should have a plan for your route, give yourself more time to get to the interview, and prepare for unforeseen delays. Body language is important. You should smile when you are greeted, and keep in mind that the interviewer is a regular person like you, and they could be nervous as well.
Don't miss our article on Electrical Technician job description.









X Cancel