Quality Inspector 2 Job Description
Quality Inspectors, Quality Control Inspectors, Quality Control Inspectors, A Job Description for a Quality Inspector, Quality Control Inspector II, A Quality Inspector's Guide and more about quality inspector 2 job. Get more data about quality inspector 2 job for your career planning.
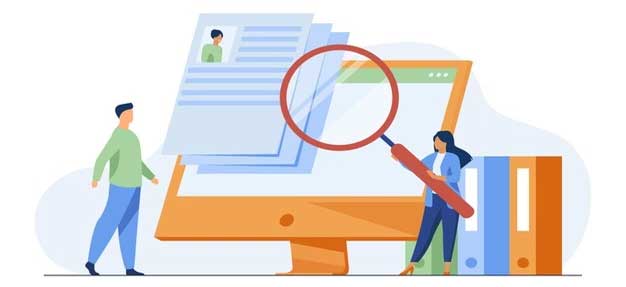
- Quality Inspectors
- Quality Control Inspectors
- A Job Description for a Quality Inspector
- Quality Control Inspector II
- A Quality Inspector's Guide
- Degrees in Quality Control Inspection
- How to Write a Resume for Quality Control Inspector
- Time Management for Software Quality
- The State of the Art: Employment Opportunities for Quality Control Inspectors
- How Much Does a Quality Control Inspector II Make?
Quality Inspectors
A Quality Inspector is a person who checks a product to make sure it meets all quality standards before it goes to market. They test the product, ensure customer specifications are met and certify the product is up to industry standards. Entry-level candidates may have two years of experience, while a more experienced Quality Inspector may have two to four years of experience.
Quality Inspector positions require a strong belief in product integrity and customer service. Experience in customer service roles such as a Salesperson or Inventory or Inspection Specialist is helpful. A candidate needs to know the industry in which the company is based and the types of products they produce.
The Chartered Quality Institute can be used to get relevant qualifications and earn quality certification for specific areas such as construction, supply chain and design process. Quality Control is a more managerial area that focuses on how the production of a product is managed and created. Quality Assurance focuses on the details of the product such as the materials and how it is received by the public.
A nice paper on Quality Metrology Technician career planning.
Quality Control Inspectors
If a product fails to meet the quality standards, it will affect the business sales and customer satisfaction levels. Ensuring that your organization has a good quality process is important. The work process is smooth with the hiring of a quality control inspector.
A quality control inspector is hired to watch for quality issues incoming raw materials and products that are ready to be shipped. They make sure that manufactured products meet the quality standards set by the organization before being sent to customers. The quality control inspector job role involves analyzing the data and conducting tests.
They are engaged in a lot of different things, from food to electronics to automobiles. They sort out the items that don't meet the quality standards and improve the production process to reduce the chances of failure. The quality control inspectors should have a good knowledge of the types of equipment and computer programs used in the organization.
They must know technical documents and blueprints to make sure products meet quality standards. The quality control inspectors may need to train their employees. They must be able to teach employees how to prevent flaws and work towards a smooth process.
A quality control inspector should be aware of the differences in products to meet the standards. They must be aware of the changes. Quality Control Inspectors can progress in the field as a trainer, team leader, and supervisor with experience.
Inspectors industries may have to lift heavy items all day. Workers in other industries can sit and read electronic data during their shift. Quality control inspectors work full time during business hours, but some work evenings or weekends.
Shift assignments are usually based on the person's previous assignments. It is possible that over time will be required to meet production deadlines. The responsibilities of the quality control worker have different requirements for education and training.
Workers receive on-the-job training that lasts between 1 month and 1 year. Training for new inspectors may include the use of special meters, gauge, computers, and other instruments, as well as quality control techniques such as Six sigma. Many employers prefer to train inspectors on the job, which is why postsecondary training programs exist.
The Holland Code framework states that quality control inspectors have an interest in the Building, Thinking, and Organizing interest areas. The focus of the Building interest area is on working with tools and machines. The thinking interest area focuses on researching, investigating and increasing the understanding of natural laws.
The focus of the organizing interest area is to keep things orderly. If you don't know if you have a Building, Thinking, or Organizing interest that would fit with a quality control inspector career, you can take a career test to see if you have what it takes. Automation is not always a substitute for inspecting by hand.
Read also our column on Software Engineer In Quality job planning.
A Job Description for a Quality Inspector
Quality Inspector makes sure incoming and outgoing products are in line with quality standards. The Quality Inspector is known as a Quality Control Inspector. They can conduct tests.
They can look at measurement. The inspector is in charge of the production processes. The quality inspector works in the production department and must have strong analytical skills.
You will be able to ensure the safety of the products. They are in charge of the production team. The inspector looks at the different workers in the production team.
Quality standards are complied with by the firm. Ans. Quality inspectors can be hired through professional networking sites or groups, if they are advertised on various job sites.
Quality inspectors are recruited through employee referrals. Ans. Product quality is important in a business scenario.
Quality Control Inspector II
Quality Control Inspector II performs quality control checks and tests. At different stages of production, the inspector inspects materials, parts and products. Being a Quality Control Inspector II records observations and may make recommendations for improving processes.
Read also our story about Chief Quality Officer career description.
A Quality Inspector's Guide
A quality inspector must have good judgement, be able to make the right decision at the right time, and prioritize work to ensure excellent results are delivered. A Quality Inspector should learn how to tap into the employee's enthusiasm and motivate the staff not just with money but with a motivation that comes through the daily relationship with each employee and creating an environment that fosters employee engagement and motivation. To save time and money, and to allow the subordinates to make wise decisions, a Quality Inspector must have the skills to make the delegation work correctly.
A Quality Inspector needs to be creative in balancing scheduling and planning by clearing the air about when and who will carry out activities, so that there is a clear flow and accountability to every staff. A Quality Inspector needs to be reliable and hire reliable employees who can be counted on as beneficial to the business, building their niche as an essential element of the larger team without worrying about bringing less than your efforts. A Quality Inspector should be enthusiastic and create a friendly atmosphere that makes the staff comfortable with the surroundings, with the other employees creating a less passive working place.
A Quality Inspector needs to design ways that will drive the staff to carry out their work without wasting time by helping them understand develop their self-motivation skills that will help them to take control of many different viewpoints of their life. A Quality Inspector should organize the work for the employees to make sure they are organized and handled efficiently by each employee for both personal and professional growth. Quality Inspectors should hire employees who use clear, logical steps and excellent judgment to understand an issue from all angles before executing an action that is in line with the company's objectives and methodical approaches to benefit productivity.
Degrees in Quality Control Inspection
Quality control inspection is very important in any manufacturing industry. It is a big part of customer maintenance. Quality control inspector in an organization is supposed to make sure that better quality measures are taken to get the best end products.
Many processes are passed before the end stage of the required products. The quality control inspector's duties begin at the base to the finish line of the production process. The job description for a quality control inspector in manufacturing outlines their responsibilities and work shifts.
Common duties include performing tests, implementing safety practices, taking measurements, maintaining records, interpreting blueprints, and fulfilling work orders. The next step is to get a degree. An associate degree will give you less edge in the job market than a bachelor's degree.
Read our report about Junior Quality Assurance job guide.
How to Write a Resume for Quality Control Inspector
A quality control specialist with over two years of experience has a detail-oriented quality control philosophy. New guidelines cut inspection time by 30%. Seeking to become the next supervisor at Queens Industrial.
A quality control inspector is a management level employee who oversees the quality checking process, the safety of manufactured products, or the readiness of software, in addition to supervising the tasks of other QC employees. How to write a resume with no experience in quality control? It is the same thing.
When writing your work history entries, think about the most relevant bullet points from the QC. There is no way to quantify soft skills, but the hiring managers know that every candidate adds them. The quality control resume should include the hard skills they ask for in the job description.
Time Management for Software Quality
Managing your time well will ensure you have enough time to complete your tasks and confirm they comply with specifications. It reduces stress and makes it easier to complete your duties. When you meet your deadlines, you also make sure others who rely on you have enough time to meet their own deadlines without affecting their work quality.
Problem-solving skills can help you find solutions if you are struggling to meet quality standards. When challenges arise in your duties, a combination of creativity, logic and critical thinking can serve you. Communication skills that are strong can help you explain how to improve processes to other people.
Your listening skills are important for understanding what your colleagues need from you. Strong written communication is a must for software testing and other quality assurance roles. Quality assurance requires understanding quality standards.
Employees are expected to work within the company's standards. Understanding the guidelines set by the Food and Drug Administration can help you meet quality expectations. Supplemental training can teach you new practices and remind you of some techniques you may have overlooked.
Don't miss our study about Medical Assistant 2 career description.
The State of the Art: Employment Opportunities for Quality Control Inspectors
Over the decade, 54,900 openings for quality control inspectors are projected, despite the fact that employment is declining. The openings are expected to be caused by the need to replace workers who transfer to other occupations or retire. Quality control inspectors had a median annual wage of over forty grand in May 2020.
Half of the workers in an occupation earn more than the median wage, and half earn less. The lowest 10 percent earned less than $26,240, and the highest 10 percent earned more than $68,220. Quality control is still not appropriate for all inspections despite technological advances.
How Much Does a Quality Control Inspector II Make?
How much does a Quality Control Inspector II make? The range for the average Quality Control Inspector II salary in the US is between 40,928 and 51,635. Many important factors, including education, certifications, additional skills, and the number of years you have spent in your profession, can affect the salary range. With more online, real-time compensation data than any other website, Salary.com helps you determine your exact pay target.
A good study about Quality Inspector career planning.









X Cancel