Safety & Safety Process Manager Job Description
Safety Managers: A Critical Role of Safety Management, OSHA Permits for Covered Process Operations, The Health and Safety Manager, Safety Management: A Multidisciplinary Approach and more about safety & safety process manager job. Get more data about safety & safety process manager job for your career planning.
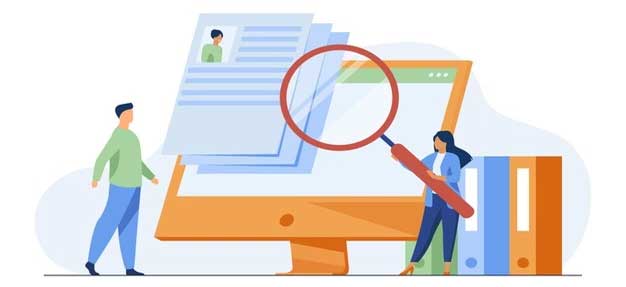
- Safety Managers: A Critical Role of Safety Management
- OSHA Permits for Covered Process Operations
- The Health and Safety Manager
- Safety Management: A Multidisciplinary Approach
- Process Safety Engineers
- Fireman Jobs, Sub Officer Job and Safety Supervisor jobs
- Communication Skills for Safety Professionals
Safety Managers: A Critical Role of Safety Management
Safety Managers are usually professionals who make sure work places meet safety and health requirements. They also give out corrective measures when needed. Safety managers have to be calm in the face of a serious crisis at work so as to prevent a panic in the organization.
See also our post on Senior Process Engineer career guide.
OSHA Permits for Covered Process Operations
Employees who operate covered processes are required to receive training from OSHA. The training should emphasize safety and health. Before starting the assignment, initial OSHA PSM training must be completed.
It is recommended that training be completed at least once every three years. A permit is needed for operations that are near covered processes. The permit must show that the fire prevention requirements were met before the start of the operation.
The permit must specify authorized work dates and locations. A report must be made to document any deficiencies. The OSHA PSM audit reports must be kept on file.
The Health and Safety Manager
The health and safety manager is responsible for maintaining minimum standards of health and safety on a premise in order to ensure that minimum standards of safety are complied with.
See also our article on Hospice Rn Case Manager career guide.
Safety Management: A Multidisciplinary Approach
You must have great attention to detail to be a safety manager. You will be able to find opportunities for improving conditions and execute safety programs. Guidelines are important for a multidisciplinary workforce.
Process Safety Engineers
They are responsible for providing process technology support to operating plants, as well as ensuring that process engineering standards and procedures are met during the development, design, and construction phases of a project. It involves assisting the Incident Investigation teams investigating and classifying process safety incidents, as well as providing support in the development of process tools and action plans to close identified Process Safety gaps. If you are applying for a job that requires a process safety engineer background, you need to show that in your resume to the recruiters that you can handle it.
Don't miss our post about Kennel Manager job guide.
Fireman Jobs, Sub Officer Job and Safety Supervisor jobs
To get Fireman Jobs, Leading Fireman Jobs, Sub Officer Jobs, Fire Officer Jobs, Fire Engineer Jobs, Chief Fire Officer Jobs, Fire Executive Jobs, EHS Officer Jobs, EHS Manager Jobs, OHS Officer Jobs, Safety Supervisor Jobs, Safety Officer Jobs, Senior Safety Officer.
Communication Skills for Safety Professionals
You need to make sure you are clear in your communication when talking about safety issues with employees. Verbal hazard communication requires precise language so people know what you are talking about. visual communications are an important part of hazard communication.
Even when you are not around, visual communications can alert people to dangers. Safety signs, vinyl labels and floor tape are some of the effective ways to communicate a hazard. Whether you are coming up with new ways of doing things, putting in new safety equipment, or just reviewing existing things with employees, you will need to provide the training that people can truly benefit from.
A high quality training program is more than just talking to employees. You need to figure out ways to get people to take safety seriously. You need to make sure that your training programs are efficient so that you don't spend a lot of time making sure everyone is aware of the latest safety initiatives.
It is important to get the most out of your budget by prioritizing different improvements. You can make major improvements to the facilities safety without spending a lot of money by investing in things like an industrial label printer. Make sure you have the budgeting skills to implement more costly improvements.
You need to be aware of all the different safety and regulatory organizations. OSHA is the most important one, but there are many others as well. Knowing the rules and regulations that will affect your facility is important when making safety improvement plans.
Read our column on Commercial Account Manager career guide.









X Cancel