Sheet Metal Worker Job Description
Sheet Metal Workers in the Construction Industry, Sheet Metal Workers at Construction Sites and Inside a Sheet Metal Shop, Sheet Metal Worker Job Description and more about sheet metal worker job. Get more data about sheet metal worker job for your career planning.
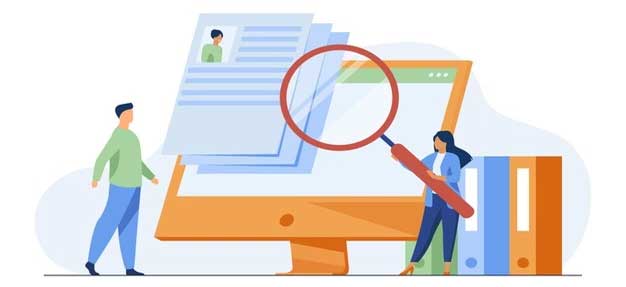
- Sheet Metal Workers in the Construction Industry
- Sheet Metal Workers at Construction Sites and Inside a Sheet Metal Shop
- Sheet Metal Worker Job Description
- Sheet Metal Workers: Salary and Experience
- Sheet Metal Workers: Apprenticeships and Jobs
- Sheet Metal Worker Jobs in the Construction Industry
- Sheet Metal Workers in the U.S
- Sheet Metal Workers in Construction and Manufacturing
- Fabrication, Assembly and Repair of Sheet Metal Products
Sheet Metal Workers in the Construction Industry
Sheet metal workers make, install, and maintain heating, ventilating, and air-conditioning duct systems, roofs, siding, rain gutter, skylights, restaurant equipment, outdoor signs, railroad cars, tailgates, and many other products made from metal sheets. They may work with plastic and fiberglass. Most workers do all three jobs.
Sheet metal workers do both construction work and mass production of sheet metal products. The kind and quantity of materials that sheet metal workers will need is determined by the plans and specifications they study. They make ductwork, countertops, and other custom products by cutting, bending, and fastening sheet metal.
Sheet metal workers operate equipment. They use computer-controlled saws, lasers, shears, and presses to cut, drill, and form parts. In shops without computerized equipment, sheet metal workers make the required calculations and use tapes, rulers, and other measuring devices for layout work.
They use machine tools to cut or stamp the parts. Sheet metal workers are employed at construction sites, metal shops, and manufacturing plants. Most are skilled in all three areas, though they can specialize in fabrication, installation, or maintenance.
Sheet metal workers are usually unskilled and only perform one repetitive task. sheet metal workers use specialized equipment to cut, form, and weld sheets of metal to create useful products for both commercial and industrial applications. Workers install products in the factory or sheet metal shop at construction sites.
A nice story about Freezer Worker job guide.
Sheet Metal Workers at Construction Sites and Inside a Sheet Metal Shop
A small percentage of self-employed workers can work nights or weekends to complete time-sensitive projects on a construction site or inside a sheet metal shop, but they are usually not working more than 40 hours per week. People working at construction sites don't need to change their schedules due to weather, they work inside the structure, which is usually near the end of the project. People who apply metal products to roofs or outdoor structures work around unfavorable weather conditions.
Sheet metal work is labor-intensive. Workers must lift heavy materials and equipment, stand for long periods of time, bend over, and sometimes crawl into small spaces to install products. Sheet metal workers use rigid safety practices because of the risk of burns, cuts from sharp metal, and falls at construction sites.
Sheet Metal Worker Job Description
Sheet metal workers install and sometimes fabricate thin metal sheets used in a variety of applications. They have a lot of responsibilities such as fastening metal seams, welding, bolting, and taking measurements. They install a variety of roofing and siding.
Sheet metal workers can work in factories and shops, operating equipment and creating metal sheets. Sheet metal workers need strong physical strength. They should have the correct math skills to take accurate measurements.
Read our paper on Janitorial Worker job planning.
Sheet Metal Workers: Salary and Experience
The average salary for sheet metal workers is $65,549 per year. The experience of the sheet metal worker is a factor in the salaries. The average salary for sheet metal fabricators is over 67,000 dollars per year.
The average salary for sheet metal mechanics is $81,356 per year, which is high due to their skills being in high demand. Good manual dexterity is required to cut sheet metal. They use sheet metal tools safely.
Sheet metal workers use their tools as required, thanks to their fine motor skills and hand-eye coordination. Computer technology is used a lot in modern sheet metal factories. They use computer software to design projects, regulate production and cut sheet metal to the required size and shape.
Computer numerical control cutting machines are used by sheet metal workers to gain experience. Sheet metal work requires working on metal components in a variety of sizes and shapes. Sheet metal workers find the right dimensions and angles for their components with the help of mathematics skills.
Sheet metal workers who perform accurate calculations cut waste. Sheet metal workers need to be fit to work. They can work in confined spaces or work for an entire shift standing up.
Sheet Metal Workers: Apprenticeships and Jobs
A sheet metal worker is a professional who makes, installs and reconditions sheet metal products, such as various elements that are part of the heating, cooling and ventilation systems, as well as roofing and drainage systems. Most sheet metal workers are self-employed, they work for companies that produce sheet metal or for companies that handle heating, air-conditioning and roofing jobs. Sheet metal workers can specialize in a single aspect of sheet metal work, but usually have experience in all three.
Those who work in factories are usually only good at one repetitive task and don't have the skills to move on to more complex roles. A high school degree is an equivalent for most sheet metal workers. The most important classes are usually geometry and algebra, as well as other courses like mechanical drawing, welding and blueprint reading.
Some sheet metal manufacturers sign partnerships with technical schools to teach students basic welding and sheet metal fabrication skills, which will prepare them for careers in the field. After graduating high school, the next step is to join an apprenticeship program. The programs include classroom participation and on-the-job training under the supervision of a senior sheet metal worker.
As the apprentices progress, they get hourly pay which increases. A typical apprenticeship program includes between 1,700 and 2,000 hours of training. Those who complete the apprenticeship gain crucial sheet metal working skills, such as knowing how to read blueprints, and first aid and safety practices.
Some states require specific licenses for sheet metal workers. Even if that is not a requirement, there are other certifications that can help increase an aspiring sheet metal worker's reputation, such as a welding certificate from the American Welding Society or a certification in precision sheet metal work from the Fabricators & Manufacturers Association International. Although many metal sheet workers continue working for the companies where they completed their apprenticeship, you can also look for other professional opportunities.
Detailed report on Metal Roofer Subcontractor career guide.
Sheet Metal Worker Jobs in the Construction Industry
Sheet metal workers can create ornate finished pieces from different metals. They will work with a variety of metal types, but also have the chance to work with copper, zinc and other specialized metals. Being employed as a sheet metal worker gives you the chance to work on unique and ornate products.
The chance to showcase their skills and talents is given by the unique products such as copper scupper boxes and leader heads. Many older structures require skilled sheet metal workers to be able to make pieces that can match historical features. Residential projects usually include sheet metal trim pieces for capping.
Specialty sheet metal components may be required as well. Residential trim is usually fabricated on site with portable brakes. Time on site for fabrication is not usually included in projects that include ornate leader heads and scupper boxes.
The sheet metal shop is where the fabrication takes place. Duct work can be made in a sheet metal shop and then transported to the site for installation. There are no requirements for education for Sheet Metal Workers.
The training of sheet metal workers on operating specific types of equipment may increase their skills. People looking to develop a career working with sheet metal should focus on training for soldering and welding. Basic math is important to help you progress and safely perform your job.
Sheet Metal Workers in the U.S
Sheet metal workers use thin steel, aluminum, or other alloyed metal in both manufacturing and construction. Sheet metal products include heating and air conditioning ducts. Maintenance workers repair and clean systems that use less energy.
Dust and moist material are removed and the sheet metal that makes up the ductwork is fixed. Testing and balancing sheet metal specialists ensure that the heating and cooling of the rooms is done correctly. The profile on heating, air conditioning, and refrigeration mechanics and installers has information workers who install or repair the systems.
Workers who install sheet metal at construction sites must bend, climb, and squat in a variety of awkward and high positions. Sheet metal workers are exposed to all types of weather. The work environment can be noisy or dusty.
A high school degree is required for sheet metal workers. Those interested in becoming a sheet metal worker should take high school classes. Vocational- education courses such as mechanical drawing and welding are helpful.
Most construction sheet metal workers learn their trade through apprenticeships, which include paid on-the-job training and related technical instruction. Construction apprentices learn about safety and first aid. The training may include welding.
Detailed column about Metal Shop Worker job guide.
Sheet Metal Workers in Construction and Manufacturing
Sheet metal is formed by an industrial process. It can be made of a number of metals, including steel, aluminum, iron, and copper, and is used to make pipes, tubes and ducts for heating and air conditioning systems, roofing and roof flashing, gutter and downspouts, the bodywork of cars and other motor vehicles, in sign. The bending and stamp operations are done using a mechanical or an automatic press.
Measuring instruments are used to check the accuracy and precision of the work. Assembly phase involves a range of operations, including welding, soldering, brazing, riveting and bolting. Sheet metal workers in construction work on roofing and other parts of the project, and they use hammers, drills, welding equipment and other tools to carry out repairs.
An inspection is conducted after a repair is done to make sure it has been waterproofed and sealed. Sheet metal workers are employed in plants to make sheet metal products. They work in fabrication shops, auto body shops and businesses that provide sheet metal installation and maintenance.
Shifts at continuous production plants are often shift based. The job of a sheet metal worker requires strength and endurance. Working conditions are not always easy.
Workers in production plants are exposed to high levels of safety risk, while workers on construction sites are exposed to high levels of safety risk. To reduce risk levels, applicable workplace safety and risk prevention regulations must be followed at all times. Another way for sheet metal workers to make money is to start their own business, which can be a roofing, gutter, and structural steel company.
Fabrication, Assembly and Repair of Sheet Metal Products
Fabrication, assembly, and repair sheet metal products and equipment, such as ducts, control boxes, drainpipes, and furnace casings. Setting up and operating fabrication machines to cut, bend, and straighten sheet metal, shaping metal over anvils, blocks, or forms, soldering and welding equipment to join sheet metal parts inspecting, assembling, and smoothing seams and joints of burred are all work that may be involved.
See also our paper about Therapeutic Program Worker job description.









X Cancel