Stockroom Manager Job Description
Stockroom Managers in Large Business, Stockroom Associates, Stockroom Work, Warehouse Management, The Management of Materials and Tools, The Four Primary Functions of Manager and more about stockroom manager job. Get more data about stockroom manager job for your career planning.
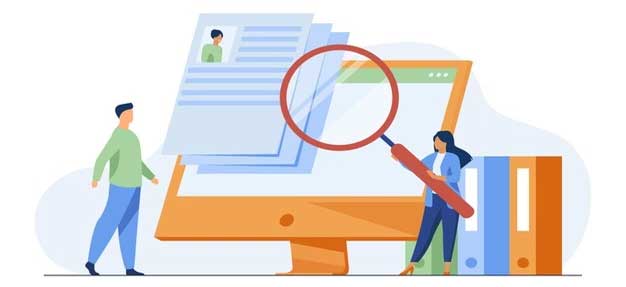
- Stockroom Managers in Large Business
- Stockroom Associates
- Stockroom Work
- Warehouse Management
- The Management of Materials and Tools
- The Four Primary Functions of Manager
- Experience in a Stockroom Assistant
- The Challenges of Warehouse Management
- Stockroom Management: How to Make Yours Run Smoother
- A Professional and Knowledgeable Assistant
- Inventory Management in a Warehouse
- A Stockroom for a Retail Store
- What Makes a Warehouse Manager?
- Performance Review Questions to Plan for the Future
Stockroom Managers in Large Business
Large businesses hold goods and supplies and Stockroom Managers are vital to that. The usual duties listed on a Stockroom Manager resume are coordinating daily operations, maintaining inventories, ordering supplies, preventing excess stock, and solving inconsistencies between inventory and stock records. Stockroom Managers should have excellent skills in computer and safety procedures. Employers look at a resume's degree in business or economics and training in accounting, administration, computer, clerical procedures, and inventory management.
Read our post about Account Manager job description.
Stockroom Associates
Stockroom associates don't usually have to work the register, since they perform the same duties as sales associates. It will depend on the job you are applying for and the company you are working for. Sales associates and stockroom associates will help customers find the products they are looking for. Stock associates work different schedules and work mostly in the stockroom handling products and shipments.
Stockroom Work
Stockroom workers receive materials into the stockroom, issue it to the production or store floor, and perform inventory transactions on the materials kept in stock. They make sure that the quantities in the inventory database are correct and that the orders are accurate. A stockroom worker needs to have basic math skills and be able to perform simple transactions on a computer.
Stockroom work can be physically demanding and may require workers to bend and assume awkward positions. Workers may have to lift heavy materials from the stockroom shelves. Workers in the stockroom must operate heavy equipment.
Don't miss our column about Field Operations Manager career guide.
Warehouse Management
The primary duty of a warehouse manager is to keep the warehouse running. Is to make sure that the activities of the warehouse staff are done in a way that doesn't cause any damage. To train staff.
The Management of Materials and Tools
To support maintenance and stores in managing materials and tools, managers must ensure that the operation has a high level of security and that any instances of theft of company property are dealt with in a manner that will discourage future theft.
Read also our paper on Operations Manager career planning.
The Four Primary Functions of Manager
The four primary functions of managers are planning, organizing, leading and controlling. Managers use the four functions to increase efficiency and effectiveness of their employees, processes, projects, and organizations. General managers, functional managers, and frontline managers are the main types of managers.
Experience in a Stockroom Assistant
A stockroom assistant is responsible for receiving and managing inventory for a store. Signing in and breaking down new shipments, sorting and inventorying goods, performing routine audits, and retrieving back-stocked inventory are some of the tasks that are done. Experience working in shipping or stock work can be considered valuable if you have specialized education. You should detail your relevant work experience and job skills in your objective statement to show why you would be a good fit for the job.
Read also our report on Hire Manager job guide.
The Challenges of Warehouse Management
A warehouse manager has three phases: receiving goods, keeping goods and distributing goods. There are many important tasks within those phases, like cataloging, storage, safety, security, coordinating with other logistics managers, and overseeing the warehouse team. A warehouse manager has to be in charge of the warehouse no matter what time it is.
They work late at night or over the weekend to make sure that high priority items can still be processed. A bachelor's in supply chain management or a related field is required to become a warehouse manager. There are many opportunities to advance, but most involve more education.
There are several layers to managing supply chains. Organization. A warehouse manager has to deal with a constant stream of items moving in and out at different rates, with different origins and destinations, and over different time periods.
It takes a highly organized person to keep track of all the relevant shipments and how they can be used to get things done. There is flexibility. Warehouse managers will be assigned unfavorable shifts early on.
A warehouse manager has to be able to operate under difficult conditions and adjust to sudden changes in the delivery schedule. The barriers to starting a low-level training job as a warehouse manager are not high. It takes a lot of experience and education to go further in supply chain management.
Stockroom Management: How to Make Yours Run Smoother
It may not be the most popular part of your store, but it is still a vital part of your location. The stockroom can help you run a tight ship. But if you mismanage it?
Your stockroom can be chaotic on the floor. Don't limit yourself to the floor. Stockrooms have high ceilings so build up.
The more items you can get onto higher shelving or rack, the more floor space you can free up for working staff to move in, which is always a plus. You can navigate the higher shelving with safe stools and ladders. If you can, place your most popular items near the front of the stockroom so that your floor staff can grab them quickly and get back to the floor.
While your employees will likely come to learn the stockroom by heart, it still takes up time and potential sales when you go into the back. Inventory management software is a great tool to help you keep your stockroom running at peak efficiency. A good stock control solution will help you predict how much merchandise you need shipped in and when, which will help ensure your stockroom never becomes overstuffed and your floor never becomes understocked.
Climate controlling your stockroom is important because it helps keep your products in perfect condition. It is important because you are going to have long hours for employees back there. Stockrooms can be dangerous and can lead to lawsuits if a customer gets hurt there.
Detailed story about Fast Track Manager job planning.
A Professional and Knowledgeable Assistant
A professional with years of experience. A skilled assistant who is focused on customer satisfaction. Excellent person who works well with others and provides accurate data for every order.
Inventory Management in a Warehouse
Stockroom management includes the receipt and storage of property, reserve space allocation for property and items, and management of specialized storage requirements. Stockroom management requires the physical upkeep of the stockroom by making sure that labels for property are posted and that property is stored in the correct location. Ensuring that all receipts are processed in a timely manner is one of the responsibilities.
Distribution activities are the majority of warehouse and logistical centers. Distribution can be a warehouse-to-warehouse transfer of property or a depot. Distribution requests are sent via computer to a storage or stockroom area.
The distribution request contains information about the item, quantity, identification, and stock number. Thelogistics specialist is responsible for ensuring the item is selected and shipped to the requester. Inventory management is the process of collecting information items that are in stock, properly identifying items and correct discrepancies related to their quantity, nomenclature, item identification and part numbers.
Management creates annual inventory schedule for each stockroom. Thelogistics specialist is responsible for physically counting and checking items in the stockroom. Special inventories can be requested when there are problems, such as an item shortage or stock number problem.
See also our story on Social Work Case Manager career planning.
A Stockroom for a Retail Store
If you aren't keeping your store busy enough, you should be keeping your stockroom as well. By keeping your stockroom organized, you will be able to replenish your inventory more efficiently, and you will be able to keep your products from getting lost or damaged. The goal should be to have a clear, visible home for all categories of merchandise and store accessories that include hangers, holiday decor, receipt rolls and much more.
There are 4. A mini fridge is a great addition to a stockroom. You can either use it to hold employees lunches or to sell it to your customers.
It is a nice addition to have. It is important to make sure it stays clean and that food doesn't rot inside. 7.
Not everything will be suitable for shelves or bins. You can prep product in the stockroom area if you have hanging racks. It can also provide a space for employee coats.
What Makes a Warehouse Manager?
It is important to find a warehouse manager. How can you be sure that a candidate is the right fit for the job? Knowing what to ask will help you find out what makes a warehouse manager tick.
You can find questions to help assess a candidate's hard skills, behavioral intelligence, and soft skills. A warehouse manager is responsible for leading a warehouse department to meet targets. Automated programming interface integration is becoming a trend, despite electronic data interchange being a standard.
A nice paper about Transportation Manager career planning.
Performance Review Questions to Plan for the Future
Performance review questions should be used to plan for the future. The person concerned and their manager should have a plan for their future. By creating a joint outlook, individual as well as company priorities are established, creating a more comprehensive work plan.
Employees dislike performance reviews because they feel like they are being unfairly treated. Everything seems to be fine until it isn't. Managers should carry out regular check-ins to overcome this.
Managers can simply have regular 1-on-1 conversations with their direct reports, even if you hold more formal check-ins with the support of a platform like Impraise. Managers can discuss any problems that have arisen with their direct reports with regular conversations. It allows people to correct in time, rather than having to look at what could have been done better at the end of the year.
It helps people have better clarity about what they are doing and what they are working towards. The end of year performance review can be checked in regularly. It allows you to be more flexible as business needs change.
No one likes a monologue when you are watching a Shakespearean tragedy. Managers dread performance appraisals because they feel the burden is on them to provide the materials for the performance meeting. It is not the template of a successful performance review.









X Cancel